Large network + Smart selection + From a single source = Online Manufacturing
As an Online Manufacturer with a network of more than 2,000 manufacturing partners, FACTUREE has access to virtually unlimited capacities for the manufacturing of all kinds of custom parts, thus securing your supply chains.
By using machine learning algorithms, we find the optimal manufacturer in terms of quality, price and delivery time for each one of your projects - from prototype to series production.
FACTUREE is the sole contract partner and contact throughout the whole duration of the project and takes full responsibility for on-time delivery and quality of the parts.
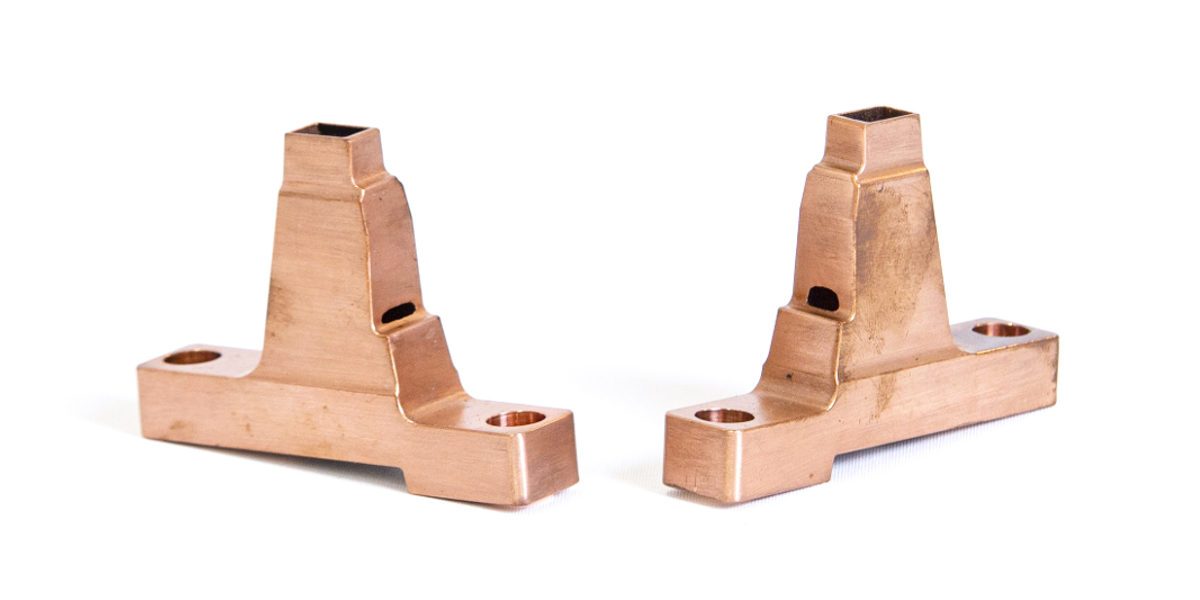
How Online Manufacturing at FACTUREE works
Inquiry
- Easy online inquiry
- Inquiries also possible by email
- Telephone customer service
Quoting process
- Express quotes â often on the same day
- Two-stage technical feasibility check
- Flexible offer optimization regarding price or delivery time
Order placement
- More than 2000 specialized manufacturing partners
- AI-supported selection of the optimal manufacturer
- FACTUREE is the sole contractual and contact partner
Manufacturing
- Broadest manufacturing range in the market
- Unlimited production capacity
- ISO 9001 certified quality management
Shipment
- Consistently short delivery times
- Europe-wide express shipping
- 100% climate neutral
Numerous advantages over conventional procurement of CNC-milled parts
Find out more about the advantages of Online Manufacturing and how you can benefit from it in our latest white paper âThe future of parts procurementâ
From industry to top international research â more than 15,000 satisfied customers
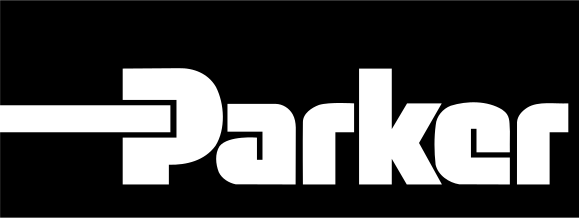
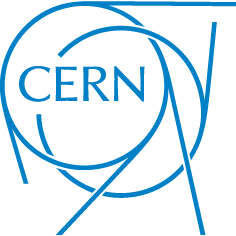


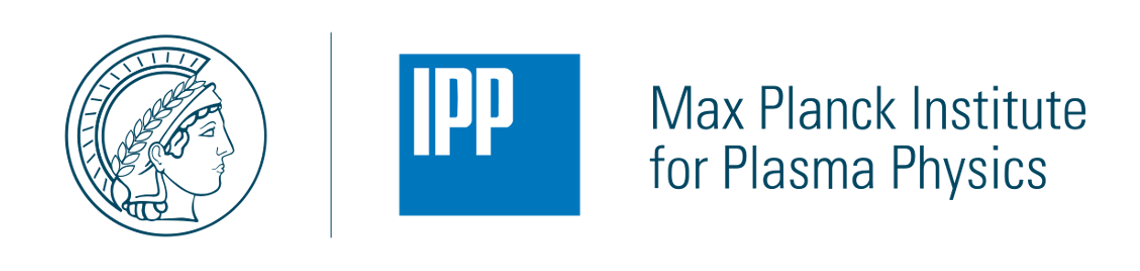
Service overview CNC milling
Manufacturing processes:
- 3-axis / 5-axis machining
- Largest material selection on the market
- Incl. surface treatments
- Prototyping and large scale mass production
Specifications for milling parts:
- Max. dimensions: L: 7500Â mm x W: 3000 mm x H: 2200 mm
- Wall thickness: from 0.2Â mm
- Quantity: starting from 1 pcs.
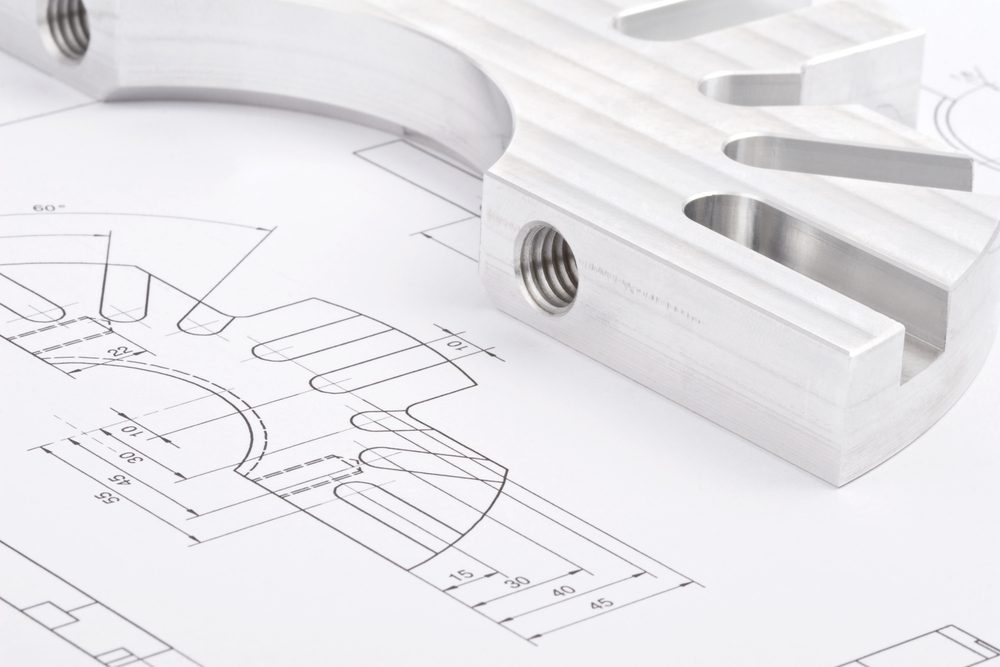
What is CNC milling?
CNC milling is a machining manufacturing process in which materials, in the form of chips, are removed from a body. In contrast to CNC turning, the workpiece does not rotate quickly around its own axis, but the milling tool which usually has several cutting edges moves to process it. The chipping of the raw piece is carried out either by driving the milling head across its surface, or by moving the body itself along a static tool.
The abbreviation CNC stands for Computerized Numerical Control and indicates that the numerical control is carried out via a computer, and that even complex workpieces can be manufactured automatically with high precision and in large quantities.Â
3-axis milling and 5-axis milling
From 3-axis milling to 5-axis simultaneous machining, FACTUREE is your one-stop shop. Due to our large production network, we cover the complete spectrum of CNC milling.
3-axis milled parts
In 3-axis milling, a drilling head works along the X, Y and Z axes - horizontally, vertically and in depth - to machine the workpiece. This way, even surfaces (e.g. grooves) and vertical bores can be created. A natural consequence of the CNC milling process is that the inner edges of a part are rounded off.
In order to avoid resulting radii impairment in the functionality of the production part, it is also possible to resort to the spark erosion (EDM) process. This process creates an electrical discharge from an electrode tool, which causes specific material evaporation on the workpiece. This also enables the creation of sharp inner edges and other shapes.
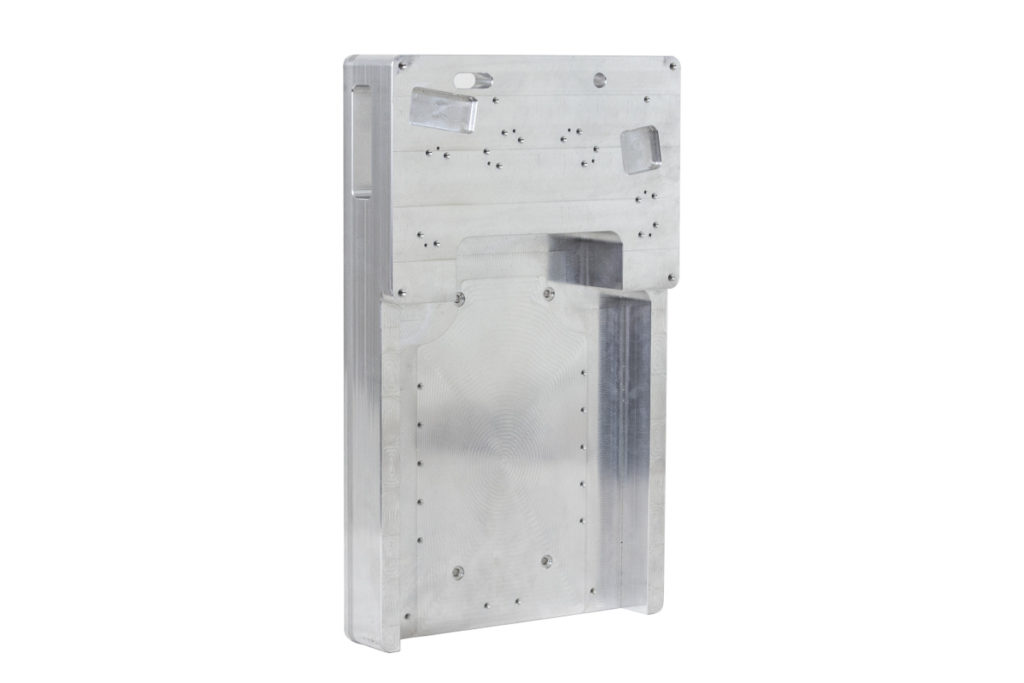
5-axis milled parts
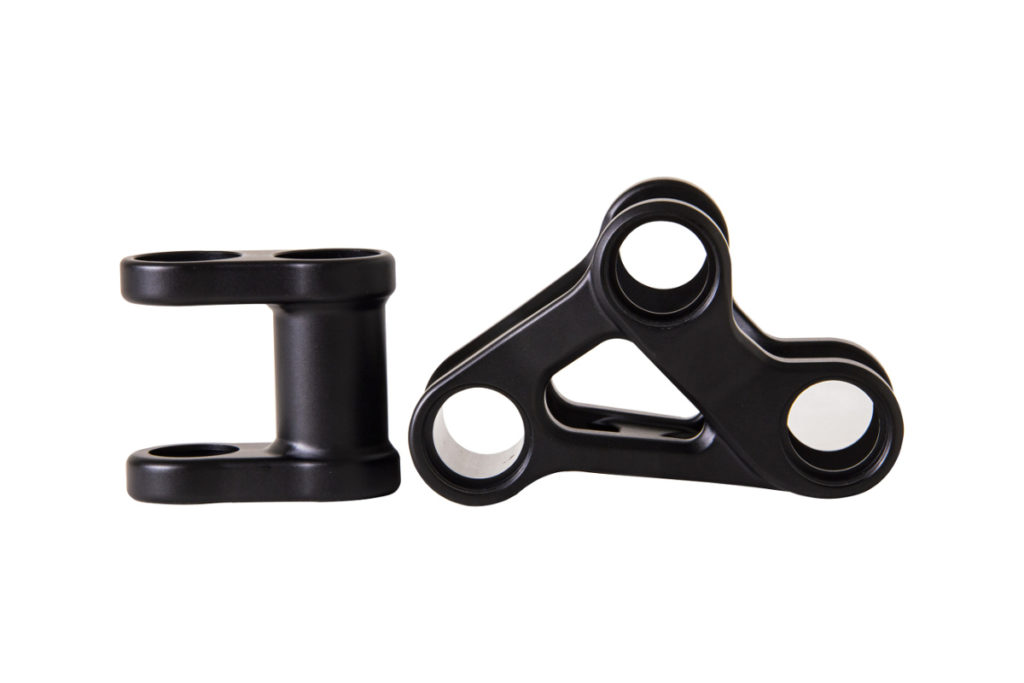
For the creation of complex geometric shapes, three movement axes often do not suffice, which is why modern 5-axis milling machines have two additional axes (A and C), in which the milling tool or alternatively the workpiece holder is rotated. The milling cutter can therefore be positioned at any angle respectively to the workpiece.
In the case of 5-axis simultaneous machining, all five axes can be moved at the same time. The workpiece can therefore usually be machined with a single operation. 3-axis milled parts can also be produced with 5-axis milling machines. In addition to the extended production spectrum of 5-axis milling, a further advantage is that workpieces can be machined from different angles, thus less time-consuming and error-prone clamping is required than with 3-axis milling.
Materials for milling
Benefit from our network with the largest material selection on the market. There is hardly any material that cannot be provided at short notice for your milled parts, and if it not possible, we almost always find a suitable alternative.
Milled metal parts
Frequently requested for aluminum milled parts:
- EN AW-5083 | 3.3547 | AlMg4,5Mn
- EN AW-5754 |Â 3.3535 | AlMg3
- EN AW-6060 | 3.3206 | AlMgSi0,5
- EN AW-7075 | 3.4365 | AlZnMgCu1,5
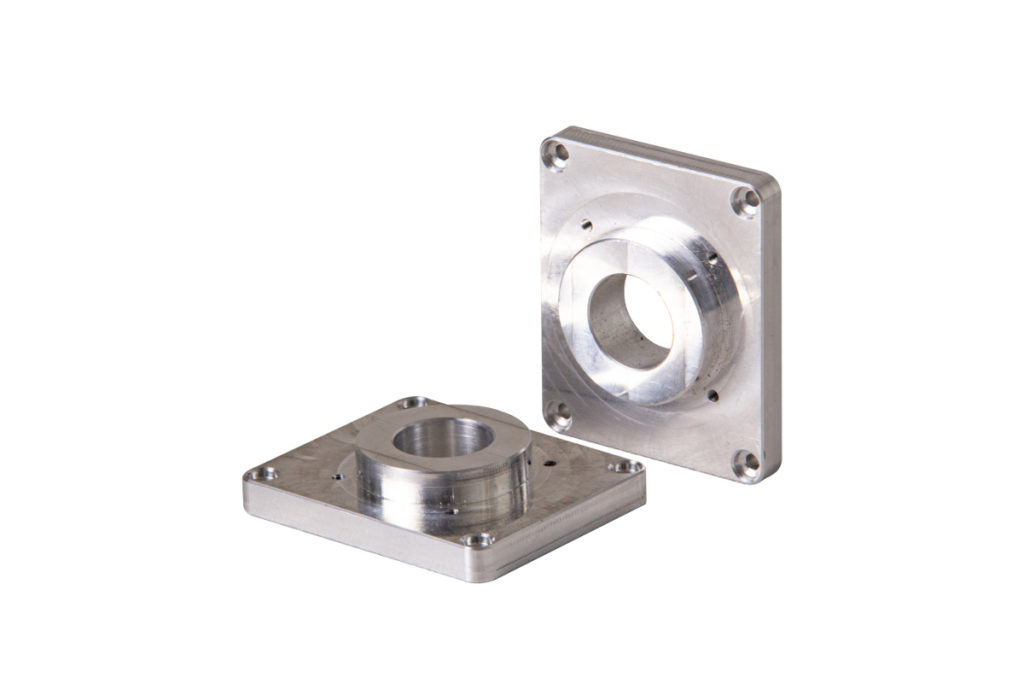
Frequently requested for steel milled parts:
- 1.0037 |Â S235JRC+C | St37k
- 1.0503 | C45
- 1.4301 | V2A
- 1.7131 | 16MnCr5
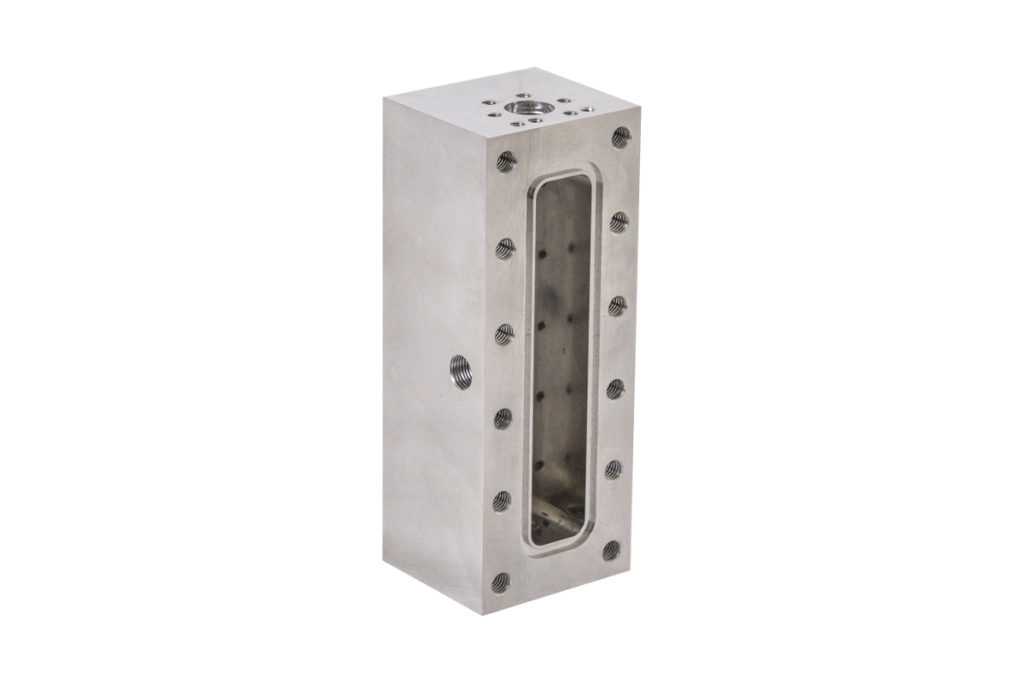
Frequently requested for:
- Copper milled parts: OF-Cu | 2.0040
- Brass milled parts: Ms58 | CuZn39Pb3 | 2.0401
- Bronze milled parts: CuSn8 | 2.1030
- Titanium milled parts: Ti Gr 5 | Ti6Al4V | 3.7165
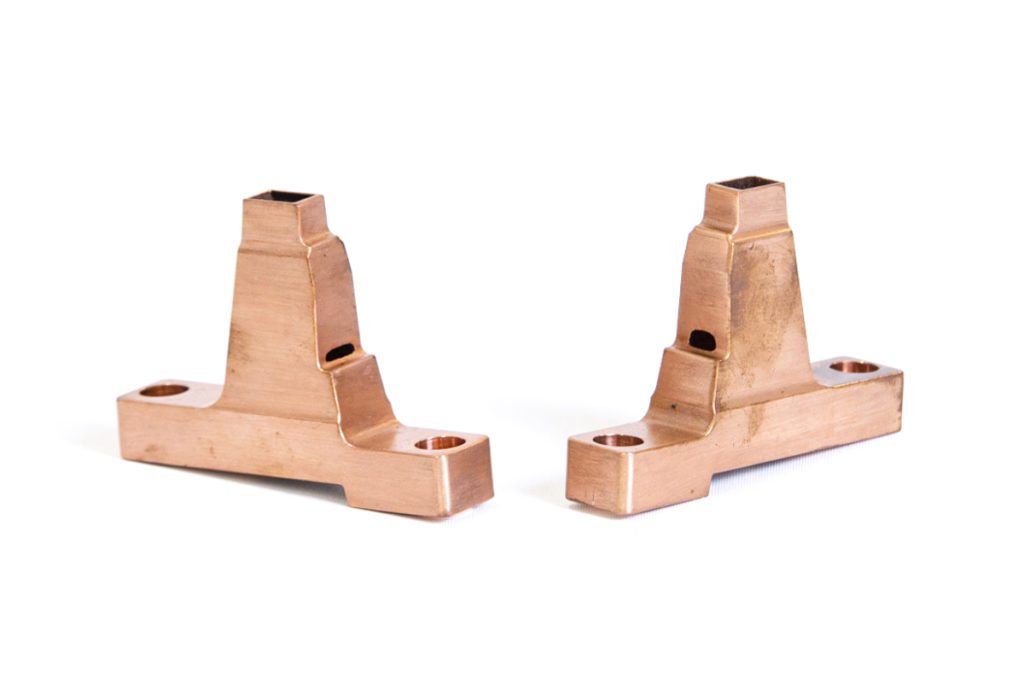
Milled plastic parts
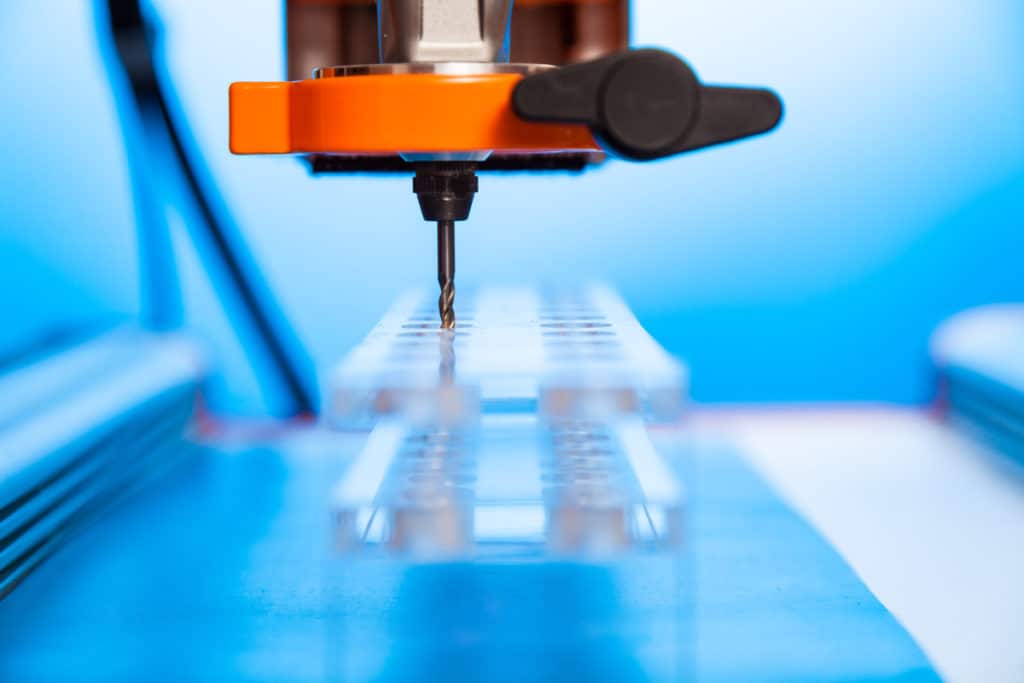
Selection of available plastics
- ABS
- PE
- PE-UHMW
- PMMA | Acrylic glass
- PVC
- PVC-U | Hard PVC
- PP
- PS
- PTFE | Teflon
- etc.
PA6
PA66 | Nylon
PBC
PC
PET
POM-C
POM-H
ESD-POM
- etc.
PEEK
PEI
PPSU
- PSU
PVDF
- etc.
- PA6 GF15
PA6 GF30
PA66 GF30
PEEK GF30
POM GF30
PP GF30
PPS GF40
- etc.
CNC-milled parts with surface treatments
By having us do the complete machining of your milled parts, including surface finishing, you save yourself the time to search for another company with free capacities. Also, you will not have to worry about the additional logistic effort. Furthermore, we remain your sole contractual partner throughout the entire manufacturing process and take full responsibility regarding the perfect quality of the milled parts and their surface finishes.
Selection of available surface treatments
- Hardening
- Quenching and Tempering
- Case hardening
- Gas nitriding
- Plasma nitriding
- etc.
- Anodizing
- Hard anodizing
- Black finishing
- Passivating
- Phosphate conversion coating
- Nickel plating
- Galvanizing (zinc plating)
- etc.
- (Laser) engraving
- Polishing
- Grinding
- Sandblasting
- Glass bead blasting
- etc.
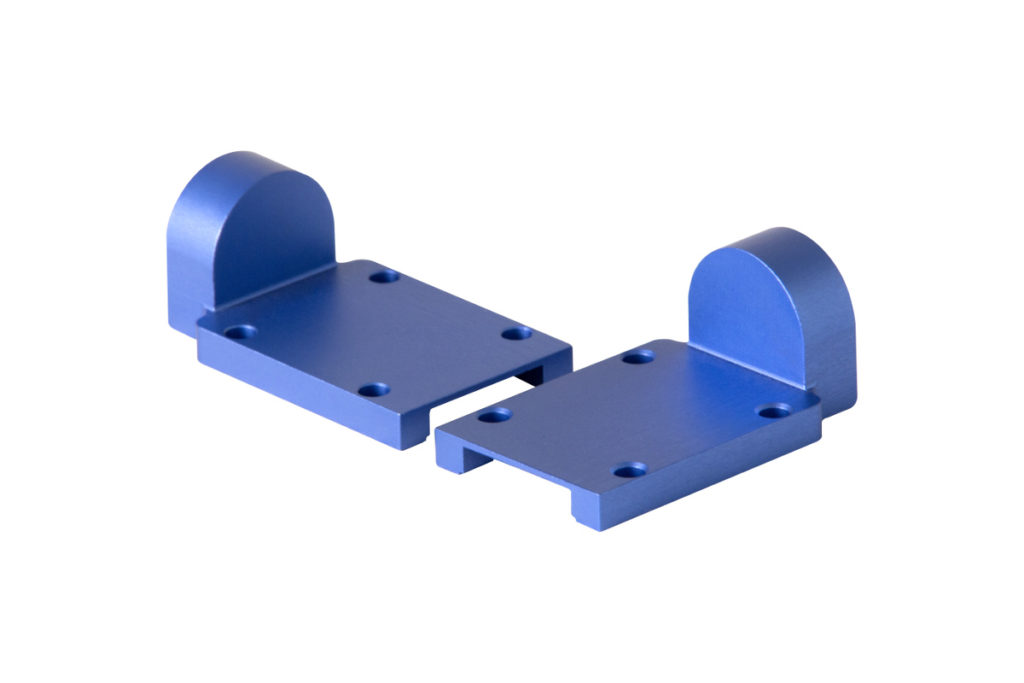
CNC milling services â from prototype to mass production
At FACTUREE you can get CNC-milled parts in all quantities, from single prototypes to mass production. Have your offer individually optimized regarding price or delivery time. We will be happy to advise you.
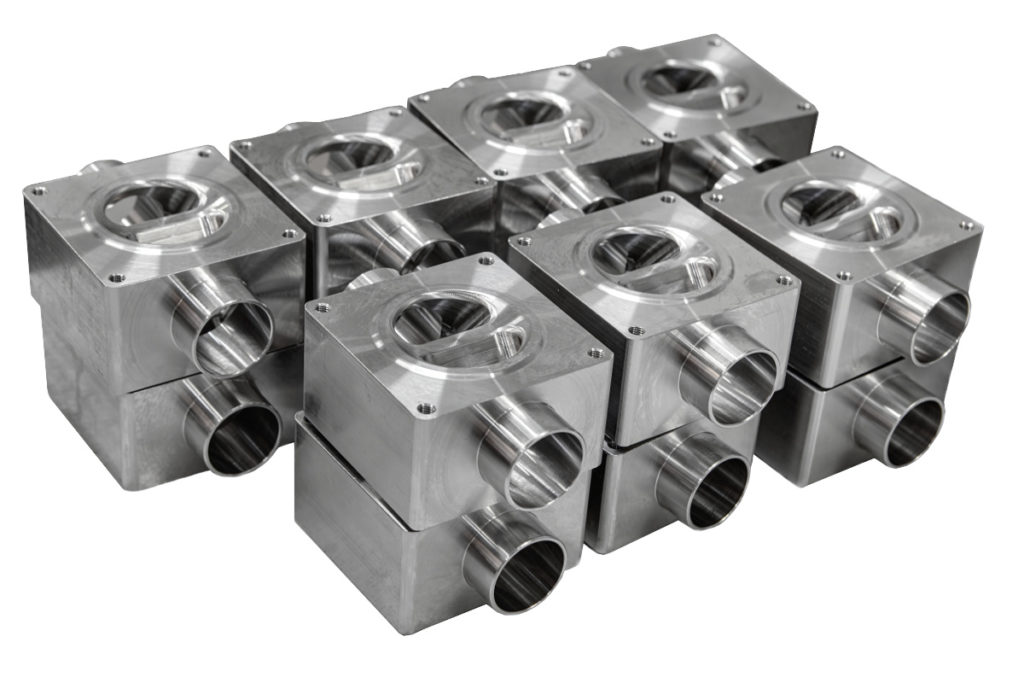
When it comes to CNC prototyping, often every day counts. Online Manufacturing has become a synonym for speed. Due to our large network of manufacturers, we always have free capacities as well as a short time delivery of 9-12 working days.Â
Also, large scale production via Online Manufacturing can have advantages. Using smart selection of a highly specialized manufacturers, it is possible to produce high quantities in a cost-efficient way. Let us check free of charge whether we can undercut your current purchase prices.
Framework agreements can offer companies long-term price stability and thus planning security. Frame contracts for CNC-machined parts can be individually designed with FACTUREE, and tailored according to your needs.Â
Case study: Festo
Festo relies on parts from online manufacturer FACTUREE to develop functional prototypes
Online Manufacturer supplies machined parts for prototypes resulting in significant time and cost savings

Pneumatic and electrical control and drive technology play an important role in factory and process automation. In this field, Festo, the worldâs leading automation technology manufacturer, supplies the market with products, systems, and services aimed at a wide range of requirements. To ensure efficient development activities including the development of new series, Festo relies on machined parts supplied by Online Manufacturer FACTUREE for its functional prototypes. The advantages: FACTUREE offers a wide range of manufacturing services, short provisioning times, and on-time delivery, enabling Festo to offer a flexible, high-quality response to the latest customer and market requirements.
Festo SE & Co. KG, headquartered in Esslingen am Neckar, is a group of companies specializing in control and automation technology. The independent family-owned multinational company supplies pneumatic and electrical automation technology to 300,000 customers in over 35 industries. With its Automation (automation technology) and Didactic (learning systems, training, and consulting) business divisions, Festo is a global leader in both automation technology and technical training.
Components for functional prototypes required on short notice
Festo regularly launches new products on the market. These innovations are subjected to preliminary analyses and extensive functional tests, using new components that are required on short notice. In order to prevent delays to its development processes and to protect its own resources, Festo sources machined components from FACTUREE â The Online Manufacturer.
Bodo Neef, Development Engineer at Festo, explains: âIn the past, we often experienced bottlenecks when procuring prototype parts, which is why we decided to hand over production of the machined parts to FACTUREE.â
FACTUREE is a brand of cwmk GmbH, which has an extensive production network that currently includes more than 500 manufacturing partners from the fields of CNC machining and surface technology with approximately 6,000 machines. All partners comply with the requirements of a continuous data-driven quality management system certified according to ISO 9001. Advantages include a comprehensive system of partners, manufacturing technologies, and surface treatments, resulting in potential for savings, increased efficiency, and more reliable delivery, as unrestricted capacities and short supply times are guaranteed.
Among other assignments, Festo entrusted Berlin-based company FACTUREE with the manufacture of machined parts, including various designs of valve blocks, for the preliminary testing of a new positioner. The project also included the complete mechanical processing of special parts.
Axel MĂŒller, a member of Festoâs positioner development team, says: âThe componentsâ requirements involve very complex contours and superior surface quality. Of all the providers we looked at, FACTUREE was the best fit for our requirements profile. We were impressed by their wide range of manufacturing methods and options as well as the guaranteed fast delivery time and straightforward quotation process. There are providers with a similar portfolio, who couldnât deliver in the short time frame we work with however.â
Online Manufacturing supports simple and fast procurement
The procurement process was very simple: 3D and 2D files created in-house by Festo were used by FACTUREE as production templates. The quote was prepared quickly. Festo was able to upload the prepared files and select the desired production method and material on the FACTUREE website.
Bodo Neef explains: âThe components were delivered on time. One version of the valve blocks we ordered performed perfectly in our functional test and could be used immediately. The other design sample was returned to FACTUREE for rework because it had a minor fault. The customer support was very positive throughout. The parts to be reworked were immediately picked up by a transport service provider commissioned by FACTUREE and, after being quickly adapted, delivered to us again.â
The components supplied by FACTUREE met all specifications and desired properties.
Future collaboration planned
As a long-standing FACTUREE customer, Festo intends to continue its relationship with the component supplier and to adapt it to future requirements as needed.
âFACTUREE takes on the task of manufacturing complex components for special applications for us, freeing up valuable resources needed for other activities. Its reliable procurement process allows us to remain operational at all times, while thanks to its extensive network of manufacturing partners, FACTUREE is always able to offer us unrestricted capacity. The very reasonable quote was also a positive factor,â concludes Axel MĂŒller.