Large network + Smart selection + From a single source = Online Manufacturing
As an Online Manufacturer with a network of more than 2,000 manufacturing partners, FACTUREE has access to virtually unlimited capacities for the manufacturing of all kinds of custom parts, thus securing your supply chains.
By using machine learning algorithms, we find the optimal manufacturer in terms of quality, price and delivery time for each one of your projects - from prototype to series production.
FACTUREE is the sole contract partner and contact throughout the whole duration of the project and takes full responsibility for on-time delivery and quality of the parts.
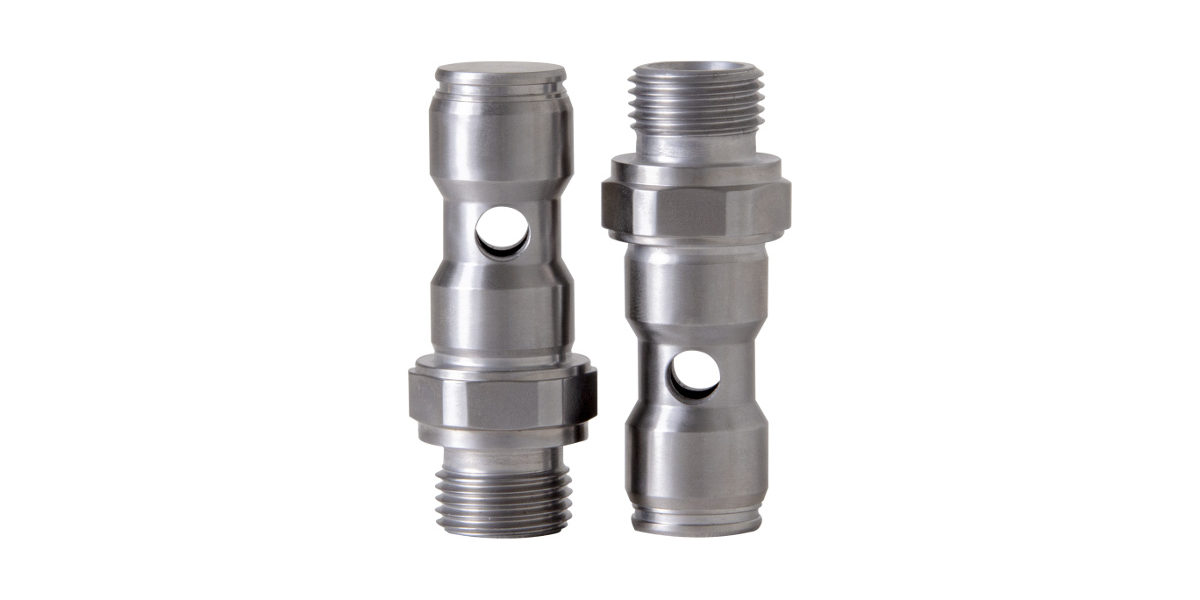
How Online Manufacturing at FACTUREE works
Inquiry
- Easy online inquiry
- Inquiries also possible by email
- Telephone customer service
Quoting process
- Express quotes – often on the same day
- Two-stage technical feasibility check
- Flexible offer optimization regarding price or delivery time
Order placement
- More than 2000 specialized manufacturing partners
- AI-supported selection of the optimal manufacturer
- FACTUREE is the sole contractual and contact partner
Manufacturing
- Broadest manufacturing range in the market
- Unlimited production capacity
- ISO 9001 certified quality management
Shipment
- Consistently short delivery times
- Europe-wide express shipping
- 100% climate neutral
Numerous advantages over conventional procurement of turned parts
Find out more about the advantages of Online Manufacturing and how you can benefit from it in our latest white paper „The future of parts procurement“
From industry to top international research – more than 15,000 satisfied customers
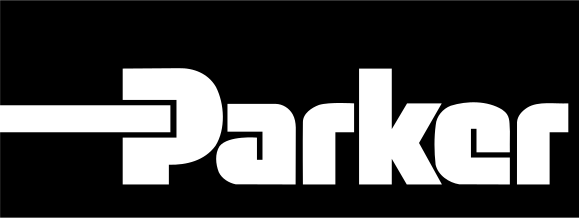
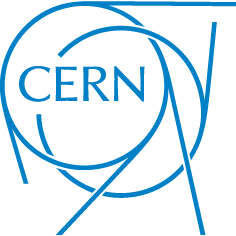


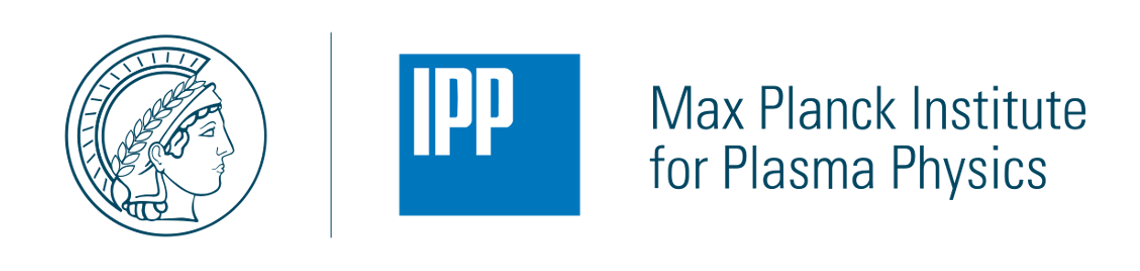
Overview CNC turning services
Manufacturing processes:
- CNC machining
- Largest material selection on the market
- Prototyping and large scale mass production
Specifications for turning parts:
- Length: 0.5 mm – 2500 mm
- Diameter: 0.5 mm – 1000 mm
- Quantity: starting from 1 pcs.
- Other dimensions possible on request
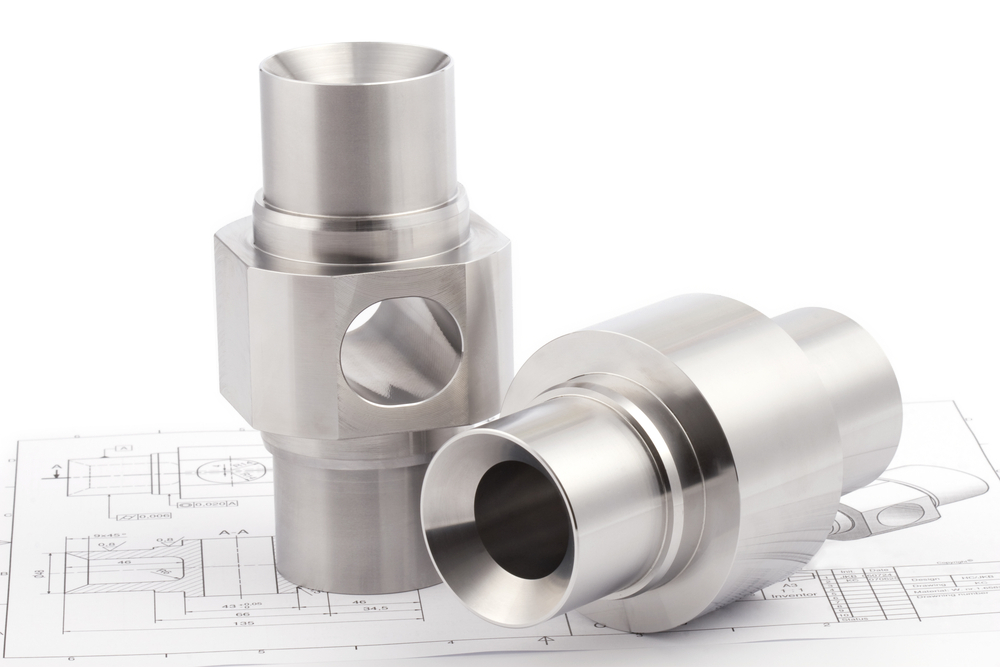
What is CNC turning?
CNC turning is a manufacturing process in which the workpiece to be machined, rotates around its own axis at high speed, while a fixed cutting tool is held against the workpiece. This tool removes material evenly, through feed movements, until the workpiece has the desired shape.
Thus, both CNC turning and CNC milling are a manufacturing process that can be assigned to subtractive manufacturing. The abbreviation CNC stands for Computerized Numerical Control, and means that the numerical control is carried out by a computer and therefore even complex workpieces can be manufactured automatically with a high degree of precision.
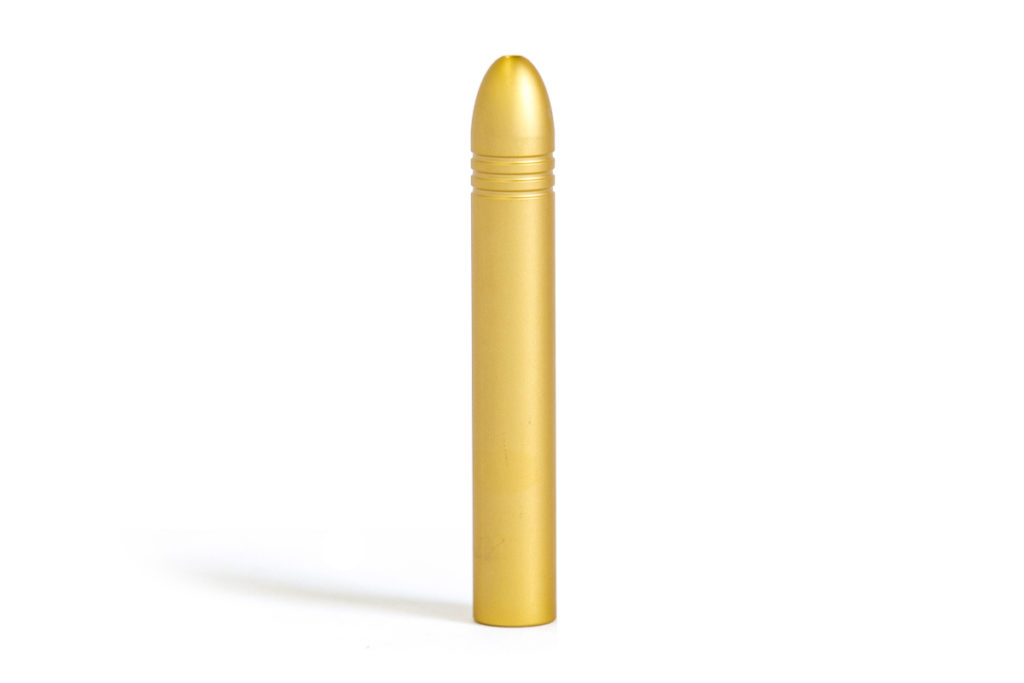
Shapes of turning parts
In contrast to CNC milling, only bodies with rotational symmetry can be generated by CNC turning. Typically, these turning parts have cylindrical or conical shapes. Planar surfaces occur only at right angles to the rotational axis, and holes are drilled along with it. If the workpiece were also to undergo additional milling or drilling work apart from the rotary axis, a lathe with a driven tool or a CNC machining center is required for machining. The process in this case is also referred to as CNC complete machining. Materials suitable for CNC turning are in particular steel, aluminum and copper alloys as well as machinable plastics.
Materials for CNC lathe machining
Benefit from our network with the largest selection of materials on the market. There is hardly a material that cannot be procured at short notice for your turned parts. If it cannot be done, we almost always find a suitable alternative.
Metal turned parts
Frequently requested for turned aluminum parts:
- EN AW-5083 | 3.3547 | AlMg4,5Mn
- EN AW-5754 | 3.3535 | AlMg3
- EN AW-6060 | 3.3206 | AlMgSi0,5
- EN AW-7075 | 3.4365 | AlZnMgCu1,5
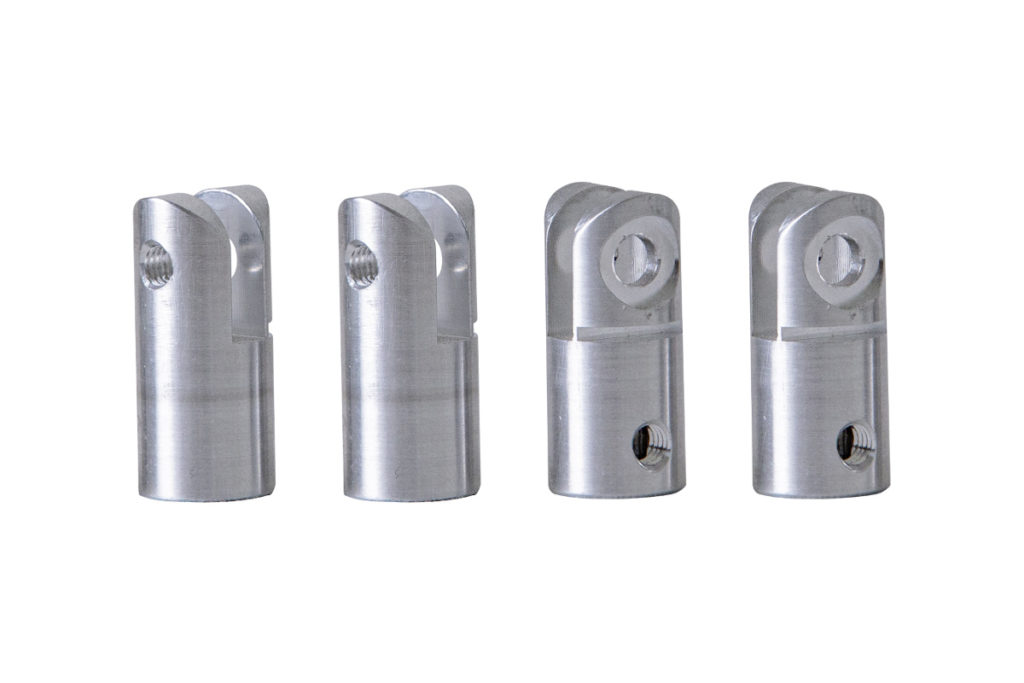
Frequently requested for turned steel parts:
- 1.0037 | S235JRC+C | St37k
- 1.0503 | C45
- 1.4301 | V2A
- 1.7131 | 16MnCr5
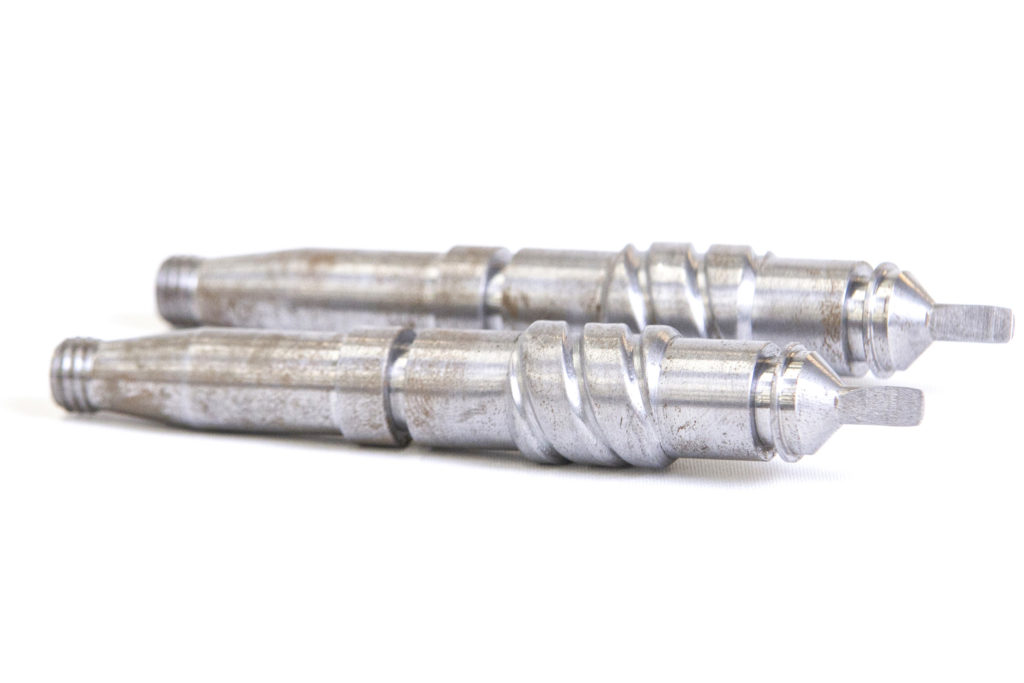
Frequently requested for:
- Turned copper parts: OF-Cu | 2.0040
- Turned brass parts: Ms58 | CuZn39Pb3 | 2.0401
- Turned bronze parts: CuSn8 | 2.1030
- Turned titanium parts: Ti Gr 5 | Ti6Al4V | 3.7165
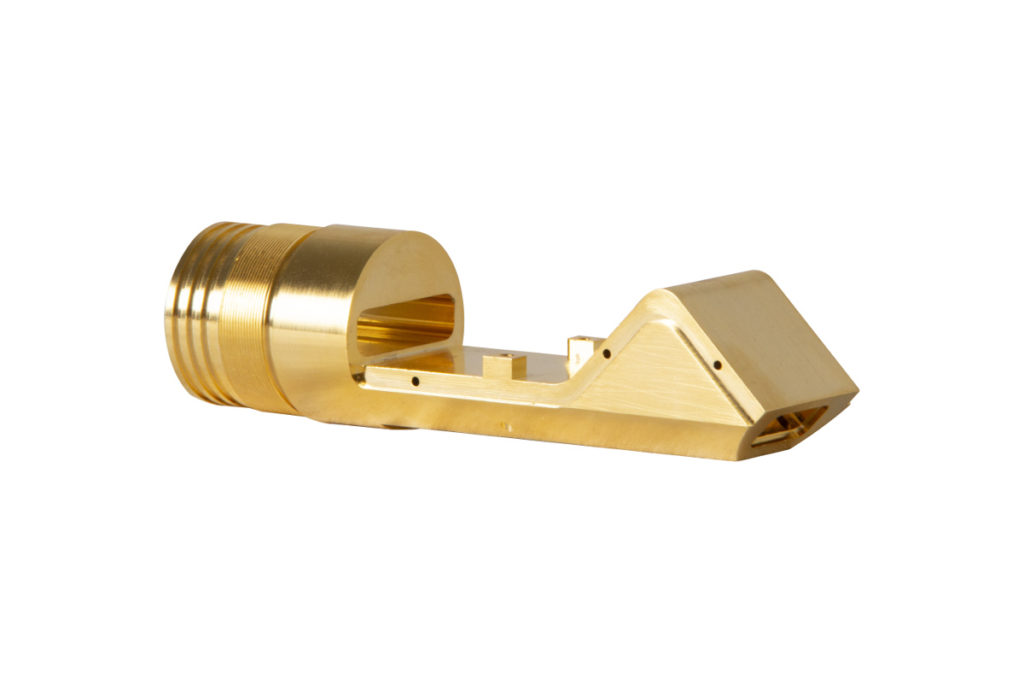
Plastic turned parts
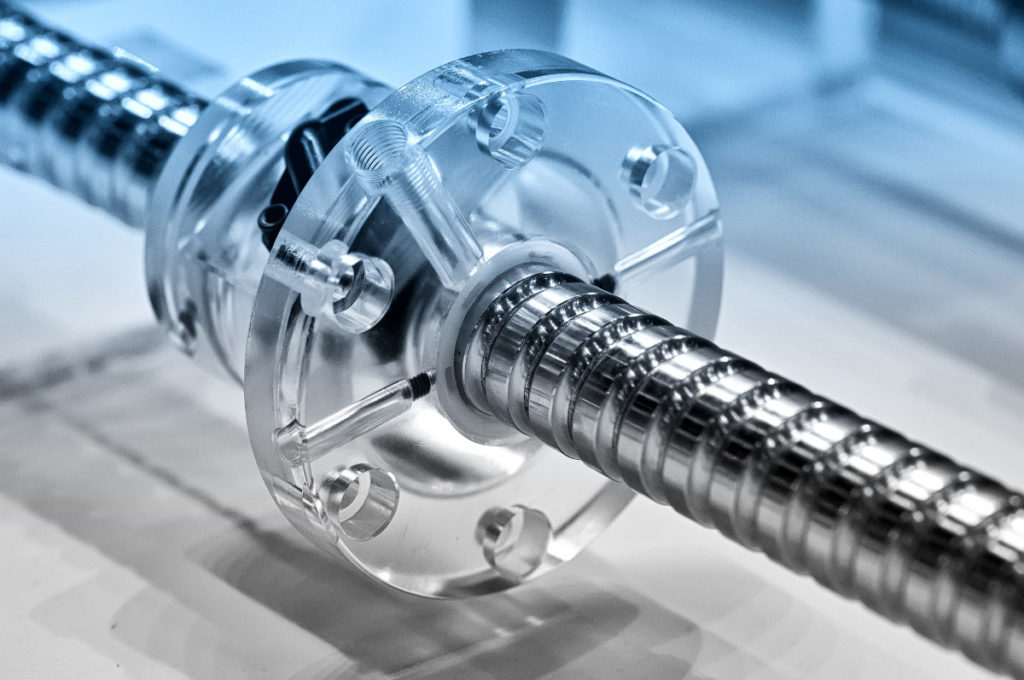
Selection of available plastics
- ABS
- PE
- PE-UHMW
- PMMA | Acrylic glass
- PVC
- PVC-U | Hard PVC
- PP
- PS
- PTFE | Teflon
- etc.
PA6
PA66 | Nylon
PBC
PC
PET
POM-C
POM-H
ESD-POM
- etc.
PEEK
PEI
PPSU
- PSU
PVDF
- etc.
- PA6 GF15
PA6 GF30
PA66 GF30
PEEK GF30
POM GF30
PP GF30
PPS GF40
- etc.
CNC-turned parts with surface treatments
At FACTUREE you can procure CNC-turned parts with surface finishes. This way, you save yourself the logistical effort of commissioning several service providers, and have only one contractual partner for the entire duration of the manufacturing process responsible for the flawless quality of the surface treatments.
Selection of available surface treatments
- Hardening
- Quenching and Tempering
- Case hardening
- Gas nitriding
- Plasma nitriding
- etc.
- Anodizing
- Hard anodizing
- Black finishing
- Passivating
- Phosphate conversion coating
- Nickel plating
- Galvanizing (zinc plating)
- etc.
- (Laser) engraving
- Polishing
- Grinding
- Sandblasting
- Glass bead blasting
- etc.
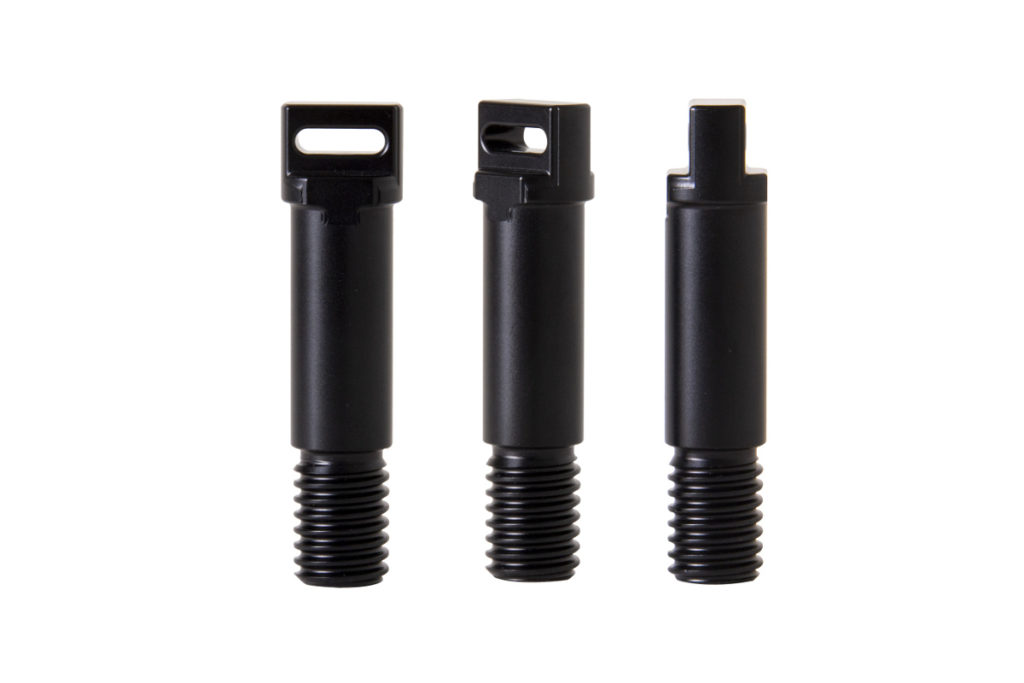
CNC turning - from prototype to large scale mass production
At FACTUREE you can get CNC-turned parts in all quantities, from single prototypes to mass production. Have your offer individually optimized regarding price or delivery time. We will be happy to advise you.
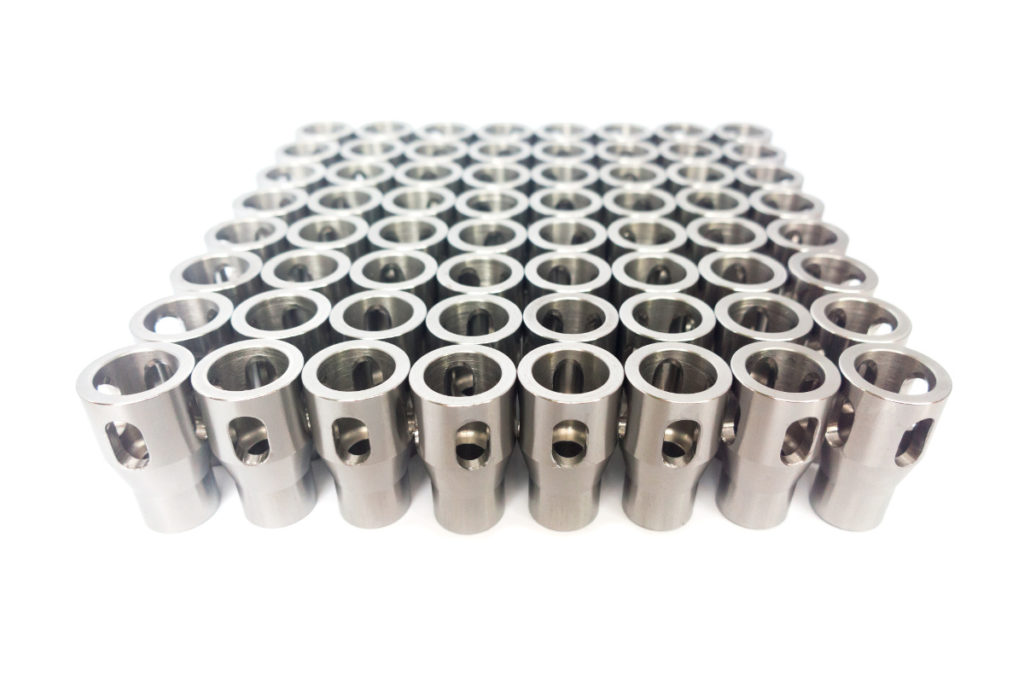
When it comes to CNC prototyping, often every day counts. Online Manufacturing has become a synonym for speed. Due to our large network of manufacturers, we always have free capacities as well as a short time delivery of 9-12 working days.
Also, large scale production via Online Manufacturing can have advantages. Using smart selection of a highly specialized manufacturers, it is possible to produce high quantities in a cost-efficient way. Let us check free of charge whether we can undercut your current purchase prices.
Framework agreements can offer companies long-term price stability and thus planning security. Frame contracts for CNC-machined parts can be individually designed with FACTUREE, and tailored according to your needs.
Case study: Parker Hannifin
Parker Hannifin relies on state-of-the-art online manufacturing of turned and milled parts by FACTUREE
Leading motion and control technology manufacturer benefits from short delivery times, unrestricted capacity and high-quality components
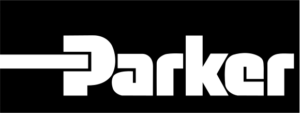
In the production of individual components, high precision and fast delivery times are indispensable today. Parker Hannifin, a leading mechanical engineering company, has opted for a modern form of procurement: Online Manufacturing of turned and milled parts.
The online manufacturer FACTUREE offers a wide production range, short response times and delivers custom components on time. Parker Hannifin is thus able to efficiently drive its own digital transformation without being affected by capacity bottlenecks and disproportionate use of human resources.
Parker Hannifin Corporation is an engineering company, founded in 1917 with headquarters in Cleveland, Ohio, USA. The company is considered a global leader in the manufacture of motion and control technologies. Parker Hannifin employs around 55,000 people in 50 countries. The worldwide corporate structure is currently divided into 139 divisions with a total of 309 branches.
Parker Hannifin, which has been operating in Germany since 1962, specialises in hydraulics, pneumatics, electromechanics, filtration, connection technology, refrigeration/air conditioning, sealing technology, aerospace and EMI shielding.
Short procurement times and high quality of components indispensable
In many companies, the procurement of turned and milled parts is a very complex process due to operational structures and special requirements. Material, processing, execution and delivery time are essential and time- and cost-intensive factors that must be well planned and usually involve many different resources such as personnel and costs. As a leading supplier in its industry, Parker Hannifin relies on short procurement times and precision workmanship for the components it needs.
Daniel Scharnowski, test bench engineer at Parker Hannifin, explains: “Until November 2019, these components were still being manufactured in Germany at our prototype department. Up to 80% of our trainees were involved in the process, which the company felt was a problem. That's why we decided to make a fundamental change at this point".
Parker Hannifin opts for efficient purchasing of components
Parker Hannifin decided to outsource the production of the parts to an online manufacturer. The end-to-end digitisation and automation of the ordering process resulting from this advanced approach to procuring turned and milled parts via an online network should lead to greater efficiency. When combined with high quality, this should give a competitive advantage.
“We obviously wanted to avoid the often time- consuming search for new manufacturers, different contacts when concluding contracts, missed delivery deadlines, etc.”, explains Scharnowski.
After an evaluation phase, Parker Hannifin chose FACTUREE, a brand of Berlin- based company cwmk GmbH. Daniel Scharnowski says: "Online manufacturer FACTUREE won us over with a quick quote and a relatively short delivery time. Ultimately, their fast response time and wide range of manufacturing services were the deciding factors”
Components for mounting devices delivered earlier than expected
Parker Hannifin first commissioned FACTUREE in November 2019 to produce special components for mounting devices in their engineering department.
FACTUREE proved the perfect choice, with its extensive production network of over 250 manufacturing partners in the fields of CNC machining and surface technology. It has over 1,500 CNC machines at its disposal at any given time. All partners comply with the requirements of an ISO 9001-certified, data-driven quality management system.
The first project was started immediately. After FACTUREE had provided a quotation, the material requisition was entered into the ERP system. As soon as Parker Hannifin received the approval from the decision makers, the order was placed via strategic purchasing. The communication between Parker Hannifin and FACTUREE was very efficient during the whole process.
The brass (CuZn39Pb3) components, divided into seven positions of 50 pieces each, were to be manufactured using sophisticated turning and milling methods, with extremely narrow tolerances of ±0.02 mm and, in some cases, additional fits. The complex manufacturing process also involved special surface treatments. The surfaces were first copper-plated, then nickel-plated in a subsequent step, before being partially polished and laser engraved.
Daniel Scharnowski sums up: “Despite the complex manufacturing process involving high quantities and tight delivery deadlines, FACTUREE was actually able to deliver the components before the agreed delivery date. In total, it took three weeks from order to delivery".
Positive experience and a vision for the future
The cooperation with FACTUREE is rated as very good by Parker Hannifin. The advantages are clearly the fast order processing, personal customer service and very short delivery times. Numerous manufacturing partners in FACTUREE's production network always offer free capacity and versatile production.
Parker Hannifin would like to further expand the cooperation with FACTUREE and adapt it to future requirements. "For future projects with FACTUREE, it would be desirable to have access to superfinishing processes such as honing, internal cylindrical grinding, roller burnishing and lapping. We would like to further intensify the cooperation in this direction", says Daniel Scharnowski.