Large network + Smart selection + From a single source = Online Manufacturing
As an Online Manufacturer with a network of more than 2,000 manufacturing partners, FACTUREE has access to virtually unlimited capacities for the manufacturing of all kinds of custom parts, thus securing your supply chains.
By using machine learning algorithms, we find the optimal manufacturer in terms of quality, price and delivery time for each one of your projects - from prototype to series production.
FACTUREE is the sole contract partner and contact throughout the whole duration of the project and takes full responsibility for on-time delivery and quality of the parts.

How Online Manufacturing of sheet metal parts works
Inquiry
- Easy upload of your 3D models and drawings
- Inquiries also possible by email
- Telephone customer service
Quoting process
- Express quotes – often on the same day
- Two-stage technical feasibility check
- Flexible offer optimization regarding price or delivery time
Order placement
- More than 2000 specialized manufacturing partners
- AI-supported selection of the optimal manufacturer
- FACTUREE is your only contract partner
Manufacturing
- Broadest manufacturing range in the market
- Unlimited production capacity
- ISO 9001 certified quality management
Shipment
- Delivery already possible after 9-12 working days
- Europe-wide express shipping
- 100% carbon-neutral shipping
The advantages over conventional procurement of sheet metal parts
Find out more about the advantages of Online Manufacturing and how you can benefit from it in our latest white paper „The future of parts procurement“
From industry to top international research – more than 15,000 satisfied customers
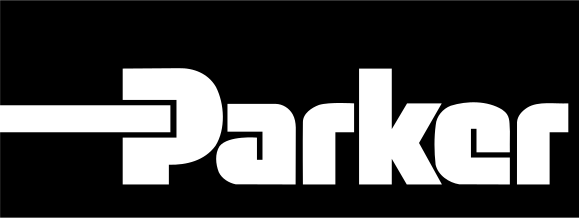
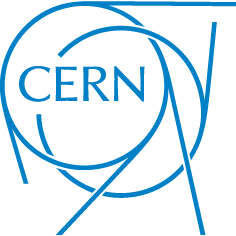


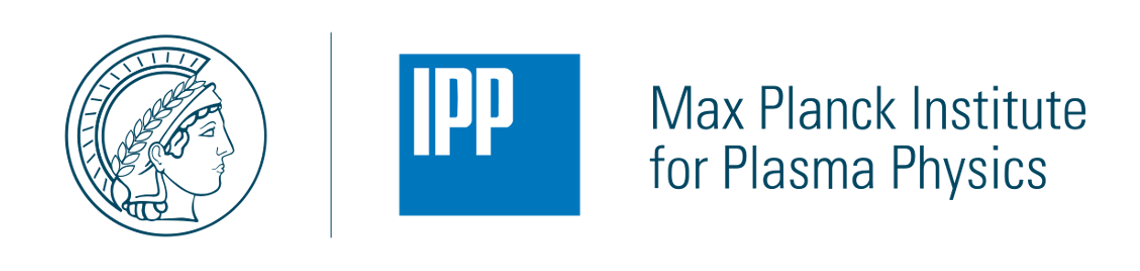
Sheet metal processing
Service range:
- All common processing methods
- Largest material selection on the market
- Incl. surface treatments
- Prototyping and large scale mass production
Specifications for sheet metal parts:
- Max. dimensions: L: 6000 mm x W: 2000 mm
- Sheet thickness: from 0.5 mm
- Tolerances: ±0.02 mm
- File formats: .stp/.step (preferred), .dxf, .pdf (optional)
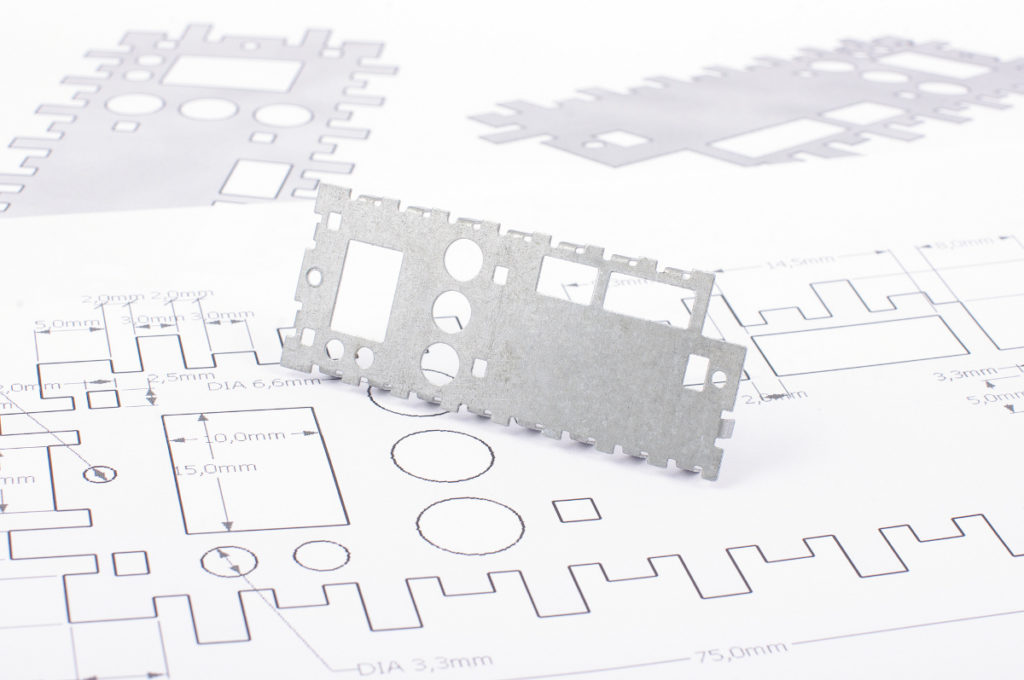
What is sheet metal processing?
Sheet metal is not a metal of its own, but rather the generic term for different types of metal that have been brought into a characteristic shape. In addition to the rectangular shape, sheet metal is characterized above all by the thickness of the material, which is significantly less than its length and width. Sheet metal is a so-called semifinished product, which is usually thin and stable, but at the same time elastic.
In order for the semifinished product to become a usable component, it must be machined. The term "sheet metal processing (or working)" therefore refers to the utilization of the starting product sheet metal by means of various processing strategies and procedures. Sheet metal processing includes the subcategories of punching, nibbling, cutting, but also forming processes such as bending, folding or deep drawing.
Various methods of sheet metal processing
Thanks to a large network of manufacturing partners, FACTUREE covers the entire spectrum of sheet metal processing. In addition, you can also get parts manufactured through CNC-milling, CNC-turning as well as 3D-printing.
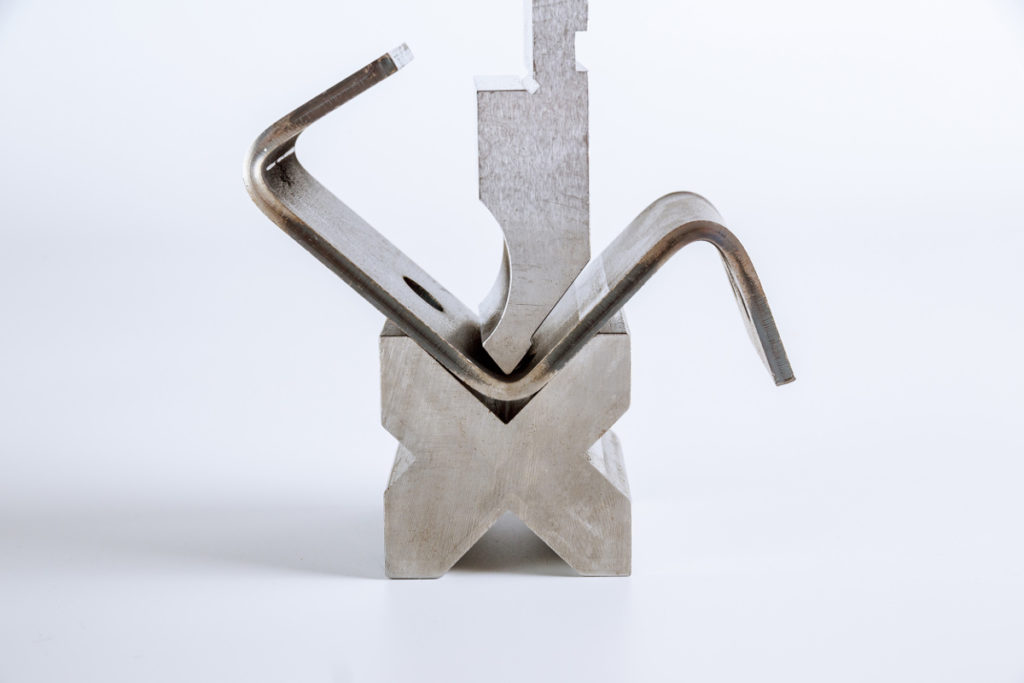
Laser cutting serves the economic, precise and fast "cutting" of workpieces from a sheet metal. For this purpose, a CNC-controlled laser is guided across the sheet metal panel. The laser beam hits the sheet metal and heats it selectively. The strong heat liquefies the metal at the specified points and thus ensures separation at the cutting edges.
Laser cutting can also be used economically with small batch sizes, enabling maximum material utilization and thus reducing waste, and offers cutting edges that do not require reworking. When it comes to cutting parts from a sheet metal without contact or force, laser cutting has become indispensable in production. Without even a single tool change, virtually any shape can be cut with a laser. The cutting edges are free from rework. In addition to sheet metal, almost any material can be cut by laser - whether it is ceramic, metal, plastic or organic material. Some disadvantages of laser cutting are: The required laser devices are cost-intensive to purchase, and the application is only suitable for thinner sheets up to a thickness of approx. 260 mm.
During water jet cutting in sheet metal processing, the sheet metal to be processed is separated by a high-pressure water jet and the admixture of cutting sand. The sheets are processed with up to 6000 bar working pressure, at the same time the sheet hardly heats up.
During water jet cutting, there is no thermal stress on the workpiece, so that almost any sheet metal can be cut with this process. The advantages of this process lie in the narrow cutting kerf width, excellent material utilization with high nesting density and correspondingly low waste as well as low environmental impact. In addition, water jet cutting is characterized by a high cutting edge quality, for which manual reworking is only necessary in rare cases. The comparatively low cutting speed and the direct contact with water - which makes water jet cutting of moisture-sensitive or rust-prone materials more difficult - can be considered disadvantageous.
During plasma cutting of sheet metal, an electrically conductive gas - plasma - is generated by means of an electric arc. The extremely high energy of the arc melts the metal at the desired location, and at the same time the molten metal is blown away by a gas jet, creating a kerf.
The advantages of this process lie in the high cutting speeds and low heat distortion. In addition to sheet metal processing, plasma can cut though most known metals, which significantly expands the areas of application. The acquisition costs for plasma torches are lower than for a laser machine, but lasers with a material thickness of 15 mm or more work faster.
During punching, components are manufactured from a sheet metal using a press and a corresponding cutting tool. This tool consists of a die and a punch, which produces the internal shape of the components.
The sheet metal is placed between the die and the punch for punching; the press presses the two parts together, and thus punches the workpiece out of the sheet metal. Punching is considered to be an extremely fast, inexpensive process, but primarily for series production. For each punched component, a separate tool must be produced, which significantly increases the price for single parts or small series. Short times and high precision of the stamped parts are also among the advantages of this process. In addition to the high tool costs, the burr caused by the punching process and uneven cutting surfaces, which make post-processing necessary, can also be considered disadvantageous.
Nibbling is another process for sheet metal processing and is closely related to punching. In nibbling, the workpiece is punched out of the sheet metal, piece by piece, through a repeated up and down movement of the tool, open on one side and with uniform feed. Cut-outs from the sheet metal can be produced without distortion by nibbling, but the cutting track punched out of the sheet metal results in greater waste compared to other processes. Nibbling makes it possible to produce even more complex shape workpieces. Nibbling also produces a burr on the parts, which must be removed after production.
CNC bending is one of the forming processing options for sheet metal. For CNC bending, the sheets are guided around a roller to produce radii. If sharp edges at a precisely predefined angle are required, sheets are bent. With the combination of CNC bending and folding, high-precision solids can be produced from sheet metal.
CNC-assisted manufacturing minimizes the error rate of bent parts, making CNC bending a convincingly efficient and cost-effective manufacturing process.
According to DIN 8584, deep drawing is the "tensile pressure forming of a sheet blank". For this purpose, the sheet is clamped on a press between the punch and die of the tool. It is important in deep drawing that the edges of the punch and die are rounded to allow the sheet to flow. Deep drawing is one of the tension forming processes in which a sheet is formed without changing the sheet thickness.
Deep drawing is considered a cost-effective, fast process - even when it comes to individual parts, prototypes or small series. Depending on the tooling required, the cost of parts produced by deep drawing is up to 60% lower than that of other manufacturing processes.
Materials for sheet metal processing
Benefit from our network with the largest material selection on the market. There is hardly a material that cannot be procured at short notice for your sheet metal parts. If it cannot be done, we almost always find a suitable alternative.
Frequently requested materials
- EN AW-5083 | 3.3547 | AlMg4,5Mn
- EN AW-5754 | 3.3535 | AlMg3
- EN AW-6060 | 3.3206 | AlMgSi0,5
- EN AW-7075 | 3.4365 | AlZnMgCu1,5
- 1.0037 | S235JRC+C | St37k
- 1.0503 | C45
- 1.4301 | V2A
- 1.7225 | 42CrMo4
- Copper: ETP-Cu | 2.0060
- Brass: CW508L | CuZn37 | 2.0321
- PMMA (Acrylic glass)
- HDPE
- POM
Sheet metal parts with surface treatments
At FACTUREE you can procure sheet metal parts with surface finishes. This way, you save yourself the logistical effort of commissioning several service providers, and have only one contractual partner for the entire duration of the manufacturing process.
Selection of available surface treatments
- Anodizing
- Powder coating
- Black finishing
- Passivating
- Nickel plating
- Galvanizing (zinc plating)
- etc.
- Glass bead blasting
- Polishing
- Electropolishing
- etc.
- (Laser) engraving
- Deburring
- Drilling
- Countersinking
- Thread cutting
- Reaming (fitting)
- Stud welding
- Pressing in
- etc.
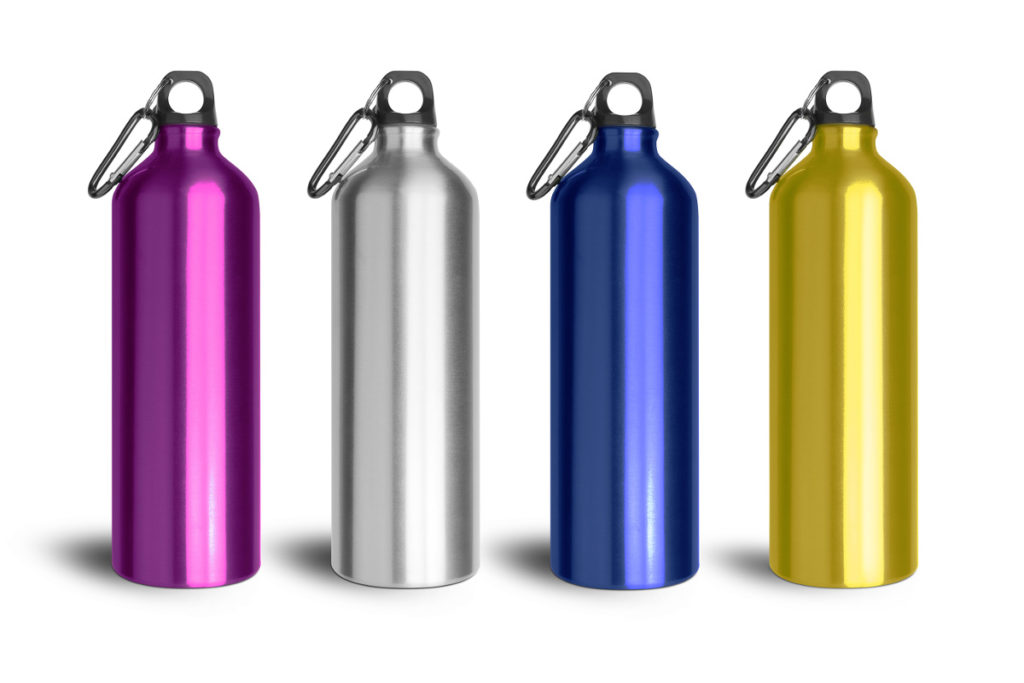
Sheet metal fabrication - from prototype to large scale mass production
At FACTUREE you can get sheet metal parts in all quantities, from single prototypes to mass production. Have your offer individually optimized regarding price or delivery time. We will be happy to advise you.
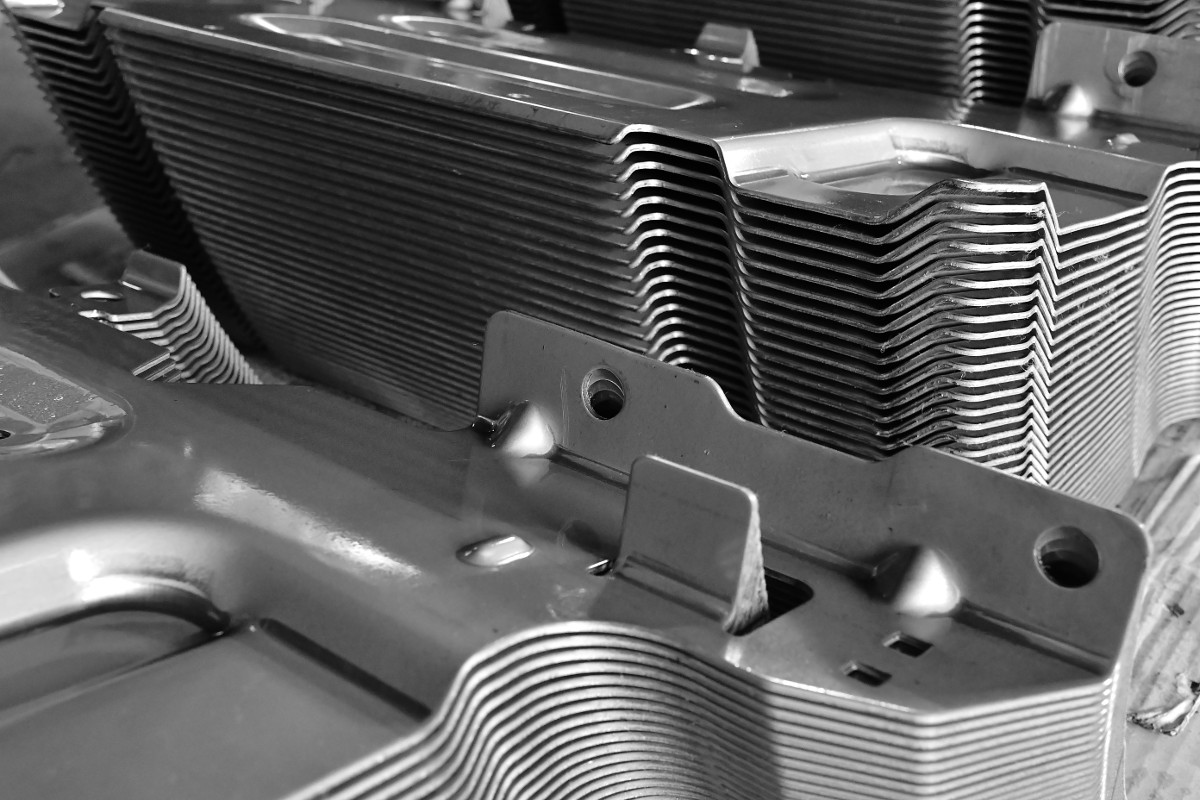
When it comes to prototyping, often every day counts. Online Manufacturing has become a synonym for speed. Due to our large network of manufacturers we always have free capacities and short delivery times of 9-12 working days.
Also large scale production via Online Manufacturing is advantageous. By the smart selection of a highly specialized manufacturers it is possible to produce in high quantities in a cost-efficient way. Let us check free of charge whether we can undercut your current purchase prices.
Framework agreements can offer companies long-term price stability and thus planning security. Frame contracts for CNC-machined parts can be individually designed with FACTUREE and tailored according to your needs.
Frequently requested materials
Case study: Freudenberg
Freudenberg Performance Materials relies on digital procurement with FACTUREE
Online Manufacturing of special parts adds benefits for textile manufacturers such as quick availability

Freudenberg Performance Materials is a leading global supplier of technical textiles. The textile solutions are used in a wide range of markets and applications. The company’s technical textiles include non-woven fabrics, woven fabrics, knitted fabrics, foams and laminates for sectors such as automotive, construction, clothing, energy, filter media, healthcare, interior finishing, shoes and leather goods, and special applications.
With more than 35 production sites in 15 countries and its headquarters in Weinheim, Germany, Freudenberg Performance Materials has a truly global presence. The company aims to be a pioneer in the development of technical textiles, modern materials and solutions, and new production methods.
Online Manufacturing as a modern procurement method
The goal of innovative products and processes is also expressed in how production partners are chosen. When implementing technical projects and maintenance work, ever shorter procurement times coupled with high manufacturing precision are crucial for success. cwmk GmbH, which operates as an online manufacturer under the FACTUREE brand name, meets these requirements with a very high level of digitalization, automation and networking as well as an ISO 9001 certified quality management system. In the broad production network, more than 8000 machines are always at the ready for projects.
“Freudenberg Performance Materials has now completed around fifteen projects with us for the external production of components. We implemented an especially large project in September of this year that included the production of several steel and aluminum milled parts as well as cut and bent sheet metal parts made of V2A stainless steel,” reports Benjamin Schwab, Head of Marke¬ting & Sales at cwmk GmbH.
Overall, most of the parts that FACTUREE produces for Freudenberg are 3-axis milled parts – some are bent parts, less frequently turned parts. The materials used are mostly steel, stainless steel and aluminum – various plastics such as PVC, PEEK and Teflon have also been used so far.
Markus Helf, Technical Manager at the Freudenberg Perfor¬mance Materials SE & Co. KG plant in Kaiserslautern, points out the advantage of the cooperation: “We highly regard FACTUREE as a reliable supplier of production parts with good delivery times and an easy-to-use procurement interface. Especially in times of coronavirus, this procurement approach offers the necessary safety. We consider this to be a good example of the advantages of digitalization, which has seen another boost during the pandemic.”