Large network + Smart selection + From a single source = Online Manufacturing
As an Online Manufacturer with a network of more than 2,000 manufacturing partners, FACTUREE has access to virtually unlimited capacities for the manufacturing of all kinds of custom parts, thus securing your supply chains.
By using machine learning algorithms, we find the optimal manufacturer in terms of quality, price and delivery time for each one of your projects - from prototype to series production.
FACTUREE is the sole contract partner and contact throughout the whole duration of the project and takes full responsibility for on-time delivery and quality of the parts.
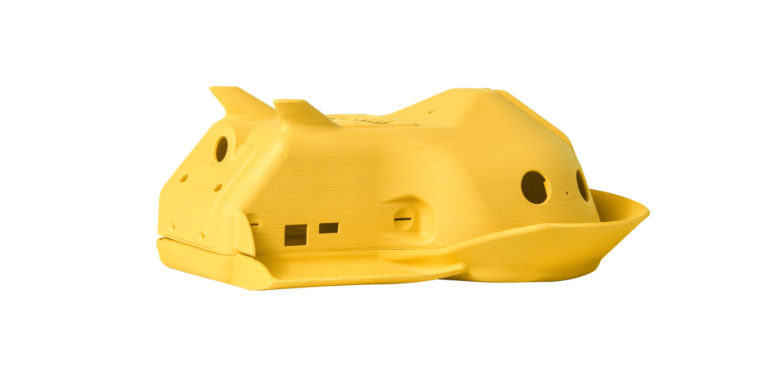
How Online Manufacturing at FACTUREE works
Inquiry
- Easy online inquiry
- Inquiries also possible by email
- Telephone customer service
Quoting process
- Express quotes – often on the same day
- Two-stage technical feasibility check
- Flexible offer optimization regarding price or delivery time
Order placement
- More than 2000 specialized manufacturing partners
- AI-supported selection of the optimal manufacturer
- FACTUREE is the sole contractual and contact partner
Manufacturing
- Broadest manufacturing range in the market
- Unlimited production capacity
- ISO 9001 certified quality management
Shipment
- Consistently short delivery times
- Europe-wide express shipping
- 100% climate neutral
Numerous advantages over conventional procurement of 3D-printed parts
Find out more about the advantages of Online Manufacturing and how you can benefit from it in our latest white paper „The future of parts procurement“
From industry to top international research – more than 15,000 satisfied customers
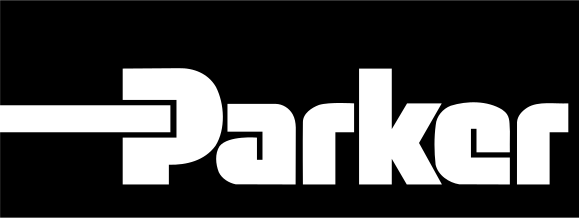
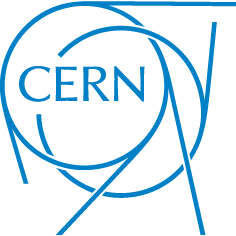


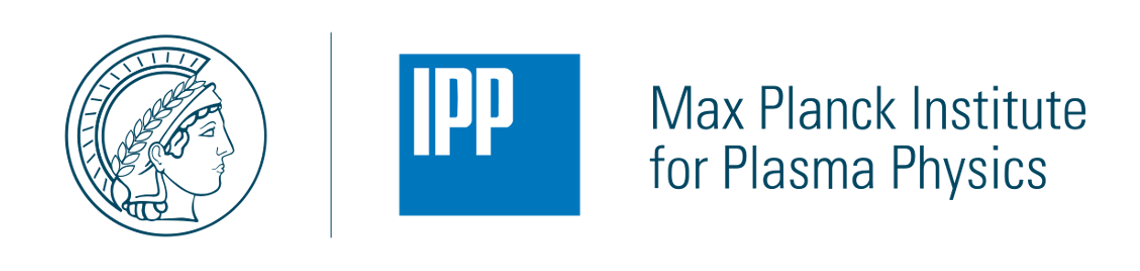
3D printing
Service range:
- all common printing processes
- Plastics, resins, metals etc.
- incl. surface finishes
- Prototyping and large scale mass production
Specifications for 3D printed parts:
- Min. dimensions: L: 3mm x W: 3mm x H: 3mm
- Max. dimensions: L: 1000mm x W: 1000mm x H: 1000mm
- Wall thickness: from 0.2 mm
- Quantity: starting from 1 pcs.
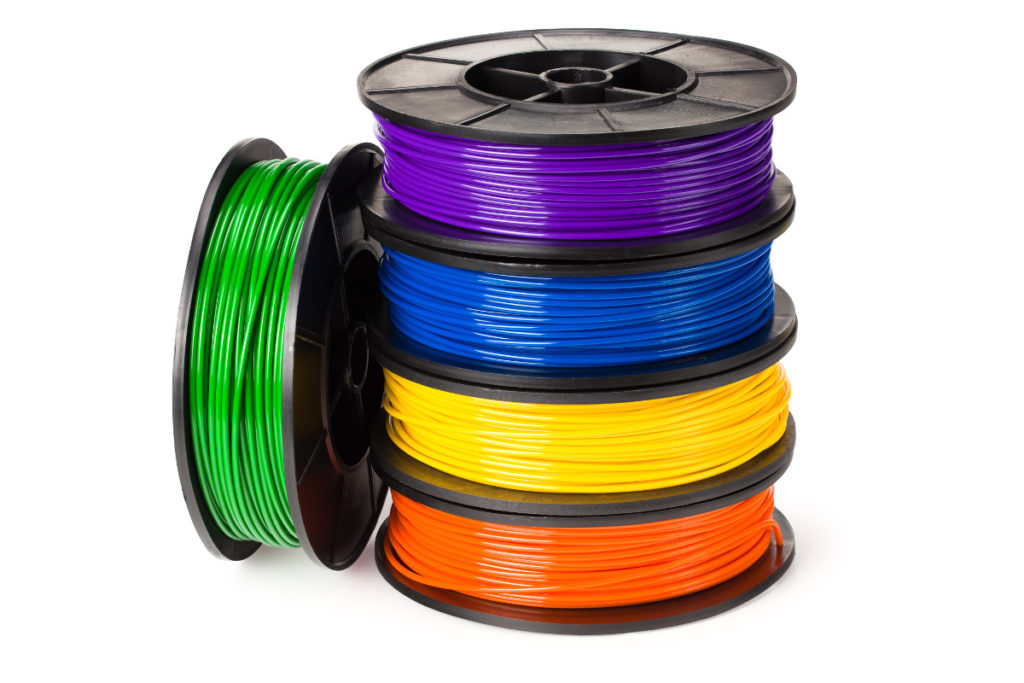
What is 3D printing?
3D printing is essentially a process in which a workpiece or a complete assembly is built up layer by layer from an original material. This process also gives rise to the term "additive manufacturing" for 3D printing. 3D printing is currently experiencing a real boom, especially in industrial manufacturing. By 2018, more than 18 billion dollars had already been spent in the 3D market worldwide - and the trend is rising sharply. In manufacturing, 3D printing has become a serious alternative to material-removing technologies such as turning and milling.
Even though the basic concept of 3D printing is always the same, there are still significant differences between the individual processes. In addition to the extrusion of materials, the curing of liquid polymers or the selective binding of material powder is also used in 3D printing.
Additive manufacturing processes
Thanks to a large network of manufacturing partners, FACTUREE covers the entire spectrum of sheet metal processing. In addition, you can also get parts manufactured through CNC-milling, CNC-turning as well as sheet metal processing.
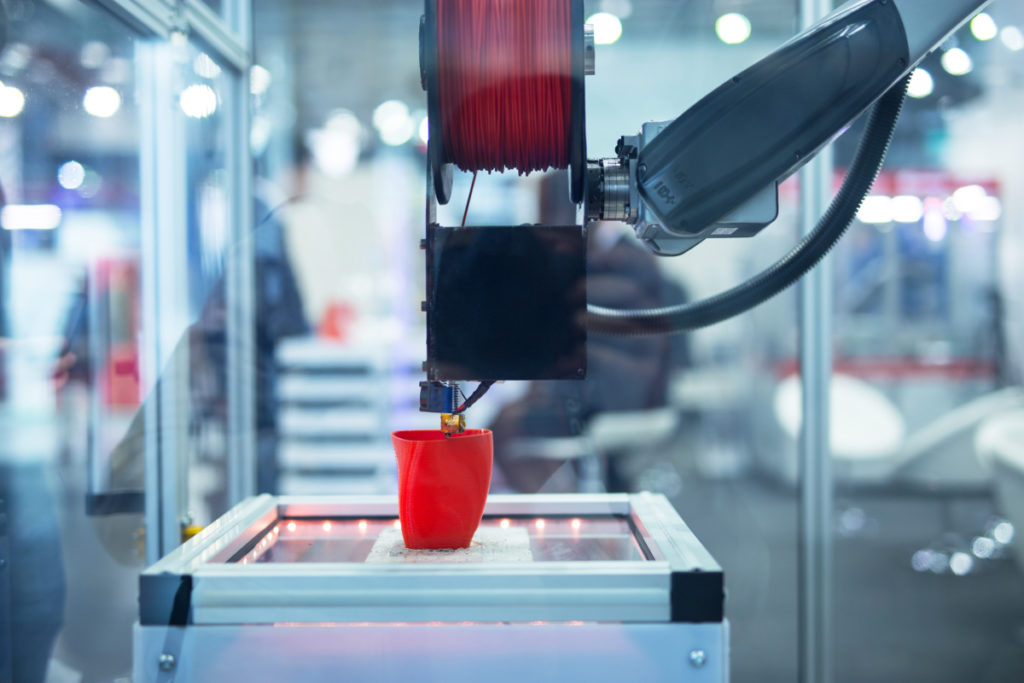
Fused Deposition Modeling is a 3D printing process in which molten plastic, in rare cases also liquefied metals, is applied layer by layer to a work platform. Layer by layer, the FDM creates a 3D print model. The basis for the FDM process is a digital 3D model which is broken down into a large number of individual layers (slices) by special CAD programs. These layers are then transferred to the working platform by the 3D printer.
The advantages of the Fused Deposition Modeling are above all in the economical, fast execution of the 3D printing. This enables short delivery times and economical printing. The printed components are also extremely dimensionally stable. A disadvantage is the low accuracy of the printed parts and the visibility of the individual print layers. With certain materials, especially ABS, thin parts can bend - the so-called "warp effect". Also in some cases, a technical peculiarity of FDM printing which can be seen as disadvantageous is that volumetric bodies are not printed solid but always with a filling structure.
All thermoplastics can be used as materials for FDM printing. ABS, polyamides, PEEK or PA6 are frequently used. Polycarbonates, PET or polypropylene are also used for FDM printing. FDM prints made of metals are still being tested. However, this has not yet been implemented on an industrial scale.
Stereolithography is the longest used 3D printing process to date. Stereolithography (SLA) was invented as early as 1983 - and is still used industrially in almost unchanged form. In stereolithography, light-curing properties of photopolymers are used to print components in 3D. The photopolymers, for example epoxy or synthetic resins, are in a liquid plastic bath. This consists of the basic monomers of the plastic. A laser is used to harden the plastics at the points specified by a CAD model. Once a layer has hardened, the working platform of the 3D printer lowers a few millimeters. A wiper distributes a new layer of liquid plastic and the laser is used again. Layer by layer, the desired object is built up.
For technical reasons, only photosensitive plastic resins (epoxy, acylate or elastomer) are used as the material for stereolithography. SLA is used for the production of filigree models, design models and prototypes, but also for the production of functional components or master models for molding. As a disadvantage, the brittleness of the objects created must be mentioned, which limits the areas of application. Since extensive reworking, such as curing the objects in a UV cabinet or manually removing support structures during SLA printing, cannot be avoided, the process is comparatively cost-intensive.
Solid components with high accuracy, high resolution and in the shortest possible time: Multi Jet Fusion is undoubtedly one of the most powerful 3D printing technologies available today. In this process, a heat-conducting liquid, the so-called "fusing agent", is applied to a layer of the material powder (usually polyamide 12). An infrared heat source is used directly afterwards. The fusing agent ensures that the area wetted by it is heated more than the rest of the material powder. This causes the material to melt together. In order to achieve sharp edges and precise contours, another active ingredient, the "detailing agent", is used. This agent is applied precisely around the areas on which the fusing agent is used. This results in a clear temperature difference - and the desired sharp edges and precise contours are created.
The advantages of the Multi Jet Fusion process lie in the almost 100 percent density of the printed components and the high printing speed. The printing speed at MJF is about 10 times higher than at other comparable processes. Due to the small droplets used in the Multi Jet Fusion for 3D printing, the resolution (1,200 dpi) exceeds any other additive manufacturing method. A disadvantage is the slightly rough surface of the printed objects and the limitation to only one material (PA 12). If colors other than gray or black are desired for the printed objects, there will be an extra cost for a coating.
The PolyJet method, also known as MultiJet Modeling, is one of the most widely used methods in rapid prototyping. For 3D printing, the PolyJet process uses a print head to apply a layered photopolymer distributed in tiny droplets to a building platform, where it is immediately cured by UV light. In PolyJet 3D printing, the finest layer thicknesses of only 16 - 32 µm are possible, which gives the models an extremely high level of detail accuracy. Smooth surfaces similar to those from injection molding are also produced. It is also no problem to combine several different materials for one workpiece with PolyJet printing. For example, solid and rubber-like materials can be combined or different materials can be mixed during 3D printing to create completely new workpiece properties. In addition to these advantages, it should also be mentioned that PolyJet 3D printing involves long printing times, which makes production quite cost-intensive. Supporting structures are also required in certain places for printing. As a result, the printed workpieces often have to be reworked manually, which also pushes up the price.
In selective laser sintering (SLS), a powdery starting material - usually polyamide or elastomer - is applied to the entire surface of the 3D printer's work platform. The powder is then sintered by a laser beam according to the specified contour, i.e. heated to just below the melting point. This causes the material to bond along the desired contour. Once a layer is finished, the building platform is lowered by the thickness of the layer. A new powder layer is applied and the process begins anew. Layer by layer and from bottom to top, the desired object is created in the 3D printer. Since overhanging structures are stabilized in the powder bed, the attachment (and subsequent removal) of support structures is not necessary. The components produced are mechanically resilient, thermostable and lightweight. SLS can also be used to print interlocked and thus movable objects. The comparatively rough surface and the long pressure cycles can be mentioned as disadvantages of the SLS process. The achievable tolerances are also higher than with other processes such as stereolithography or the PolyJet process. As already mentioned, the main material used for SLS is polyamide. Thermoplastic polyurethanes (TPU) or polyether ketones (PEK) are also used less frequently in selective laser sintering. If PA12 (nylon) is used for SLS, it can be enriched with additions to achieve specific material properties. Supplementary material is, for example, aluminium or carbon fibre.
Selective laser melting (SLM) is one of the most versatile 3D printing processes and a cost-effective alternative to welding, milling or casting. In selective laser melting, metal in powder form is applied to a building platform and then melted along the desired contour using a laser beam. SLM also works in layers, which means that the building platform is lowered after a layer is created, fresh powder is applied and then remelted. Required support structures are automatically installed parallel to the actual printing.
The advantage of the SLM is clearly its freedom of design. Since the components are built up layer by layer in the desired form, even extremely complex geometries and moving parts can be generated from materials that are difficult to machine. Selective laser melting is at the same time extremely economical due to minimal amounts of waste. The materials used are aluminum, stainless steel, titanium or cobalt-chromium alloys. Depending on the manufacturer or manufacturing company, selective laser melting is also referred to as DMLS (Direct Metal Laser Sintering), LMF (Laser Metal Fusion) or Additive Layer Manufacturing. However, the different terms all refer to the same process.
In addition to the methods commonly used in industry, there are other 3D printing possibilities. One example is 3D printing, in which gypsum-like powder is bonded layer by layer using a binder. Or Digital Light Processing (DLP), which roughly resembles stereolithography. However, a projector or LCD display is used instead of a laser to cure the base material. Electron beam melting (EBM) is also used in places for 3D printing. EBM always requires a conductive material in powder form. The material is "bombarded" with energy from electrons in the 3D printer and thus melted.
Which 3D printing process is ultimately the most economical, fastest and optimal for the respective application cannot be answered in general. Each process has its own specific advantages and disadvantages. Therefore, for each 3D print, it is necessary to weigh up which process should be selected as being most suitable.
Material Selection for 3D Printing
Benefit from our network with the largest selection of materials on the market. There's hardly a material that can't be procured at short notice for your 3D printed parts. And if it does, we can almost always find a suitable alternative.
- ABS
- PC
- PEEK
- PEI
- PET
- PETG
- PLA
- Polyamide (Nylon)
- PP
- Silicones
- etc.
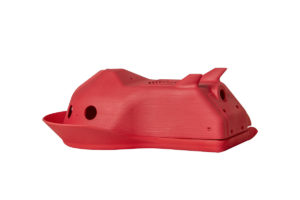
- Standard
- Clear
- Durable
- Flexible
- High Temp
- Polycarbonate-like
- etc.
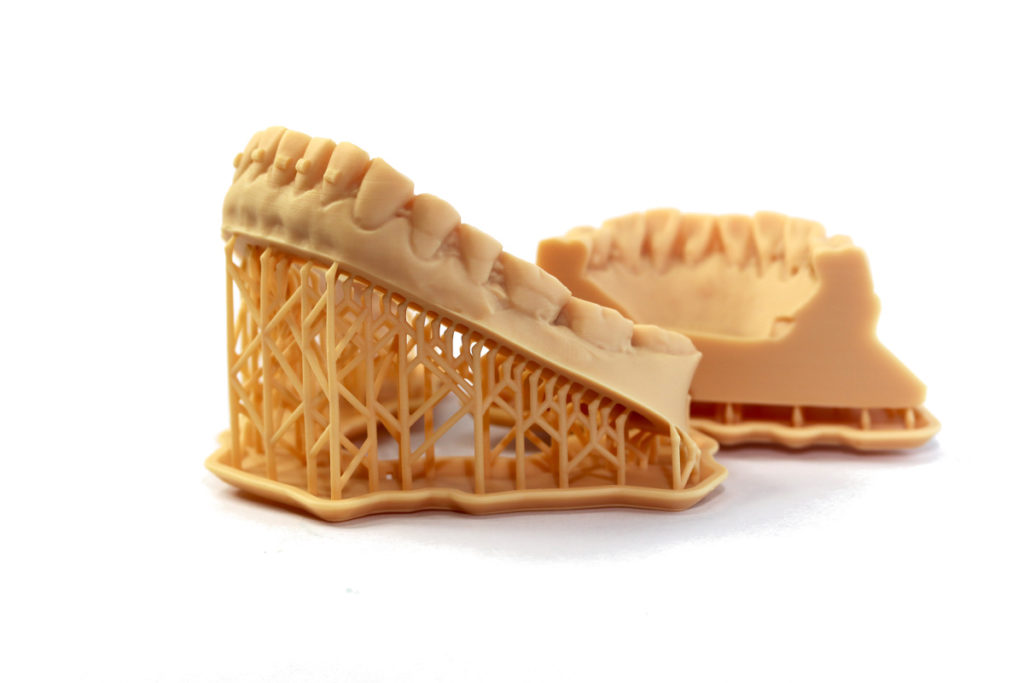
- Aluminum alloys
- Stainless steel
- Inconel
- Titanium
- etc.
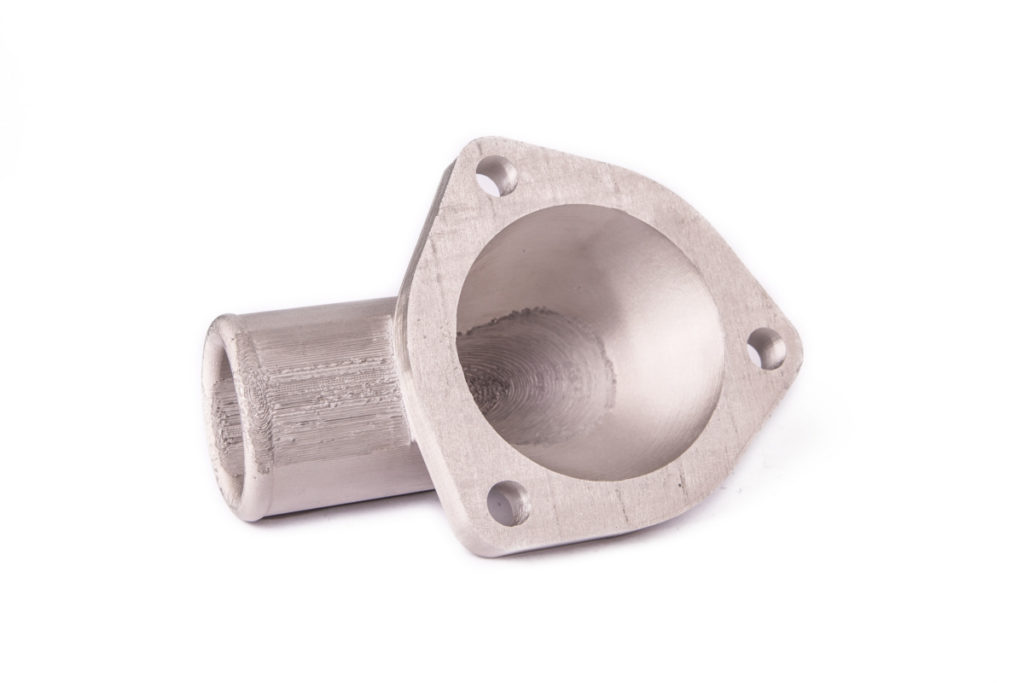
- Composites e.g. alumides
- Polymer plaster
- More materials upon request
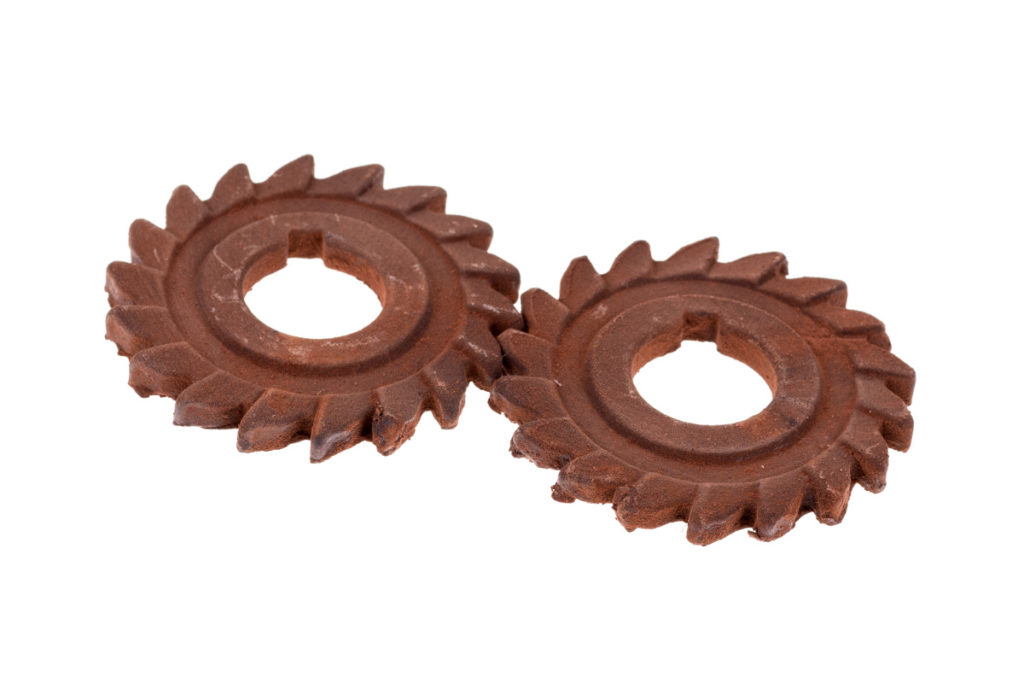
3D printing - more than prototyping
At FACTUREE, you can get 3D printed parts in any quantity, from individual prototypes to mass production. Have your offer individually optimized for price or delivery time. We will gladly advise you.
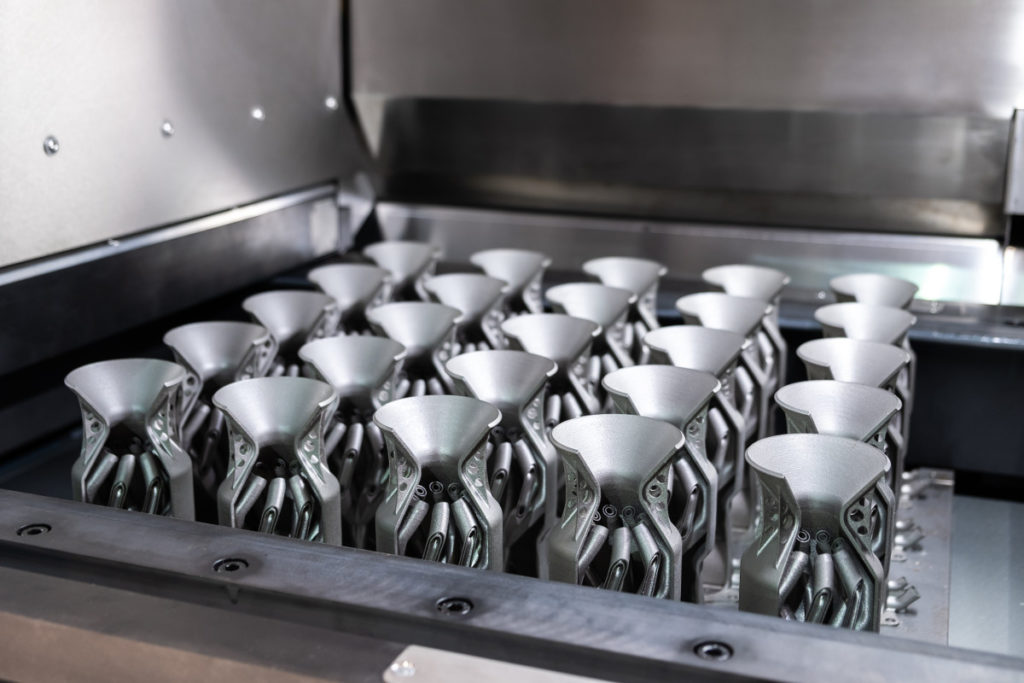
In prototyping every day counts usually. Online Manufacturing has become a synonym for velocity. Due to our large network of manufacturers we always have free capacities and short delivery times.
The procurement of serial parts via Online Manufacturing is also advantageous. The smart selection of a highly specialized manufacturer allows for cost-efficient manufacturing in large quantities. Let us check for free if we can beat your current purchase prices.
Framework agreements can offer companies long-term price stability and thus planning security. Frame contracts for CNC-machined parts can be individually designed with FACTUREE and tailored according to your needs.
Case study: Festo
Festo relies on parts from online manufacturer FACTUREE to develop functional prototypes
Online Manufacturer supplies machined parts for prototypes resulting in significant time and cost savings

Pneumatic and electrical control and drive technology play an important role in factory and process automation. In this field, Festo, the world’s leading automation technology manufacturer, supplies the market with products, systems, and services aimed at a wide range of requirements. To ensure efficient development activities including the development of new series, Festo relies on machined parts supplied by Online Manufacturer FACTUREE for its functional prototypes. The advantages: FACTUREE offers a wide range of manufacturing services, short provisioning times, and on-time delivery, enabling Festo to offer a flexible, high-quality response to the latest customer and market requirements.
Festo SE & Co. KG, headquartered in Esslingen am Neckar, is a group of companies specializing in control and automation technology. The independent family-owned multinational company supplies pneumatic and electrical automation technology to 300,000 customers in over 35 industries. With its Automation (automation technology) and Didactic (learning systems, training, and consulting) business divisions, Festo is a global leader in both automation technology and technical training.
Components for functional prototypes required on short notice
Festo regularly launches new products on the market. These innovations are subjected to preliminary analyses and extensive functional tests, using new components that are required on short notice. In order to prevent delays to its development processes and to protect its own resources, Festo sources machined components from FACTUREE – The Online Manufacturer.
Bodo Neef, Development Engineer at Festo, explains: “In the past, we often experienced bottlenecks when procuring prototype parts, which is why we decided to hand over production of the machined parts to FACTUREE.”
FACTUREE is a brand of cwmk GmbH, which has an extensive production network that currently includes more than 500 manufacturing partners from the fields of CNC machining and surface technology with approximately 6,000 machines. All partners comply with the requirements of a continuous data-driven quality management system certified according to ISO 9001. Advantages include a comprehensive system of partners, manufacturing technologies, and surface treatments, resulting in potential for savings, increased efficiency, and more reliable delivery, as unrestricted capacities and short supply times are guaranteed.
Among other assignments, Festo entrusted Berlin-based company FACTUREE with the manufacture of machined parts, including various designs of valve blocks, for the preliminary testing of a new positioner. The project also included the complete mechanical processing of special parts.
Axel Müller, a member of Festo’s positioner development team, says: “The components’ requirements involve very complex contours and superior surface quality. Of all the providers we looked at, FACTUREE was the best fit for our requirements profile. We were impressed by their wide range of manufacturing methods and options as well as the guaranteed fast delivery time and straightforward quotation process. There are providers with a similar portfolio, who couldn’t deliver in the short time frame we work with however.”
Online Manufacturing supports simple and fast procurement
The procurement process was very simple: 3D and 2D files created in-house by Festo were used by FACTUREE as production templates. The quote was prepared quickly. Festo was able to upload the prepared files and select the desired production method and material on the FACTUREE website.
Bodo Neef explains: “The components were delivered on time. One version of the valve blocks we ordered performed perfectly in our functional test and could be used immediately. The other design sample was returned to FACTUREE for rework because it had a minor fault. The customer support was very positive throughout. The parts to be reworked were immediately picked up by a transport service provider commissioned by FACTUREE and, after being quickly adapted, delivered to us again.”
The components supplied by FACTUREE met all specifications and desired properties.
Future collaboration planned
As a long-standing FACTUREE customer, Festo intends to continue its relationship with the component supplier and to adapt it to future requirements as needed.
“FACTUREE takes on the task of manufacturing complex components for special applications for us, freeing up valuable resources needed for other activities. Its reliable procurement process allows us to remain operational at all times, while thanks to its extensive network of manufacturing partners, FACTUREE is always able to offer us unrestricted capacity. The very reasonable quote was also a positive factor,” concludes Axel Müller.